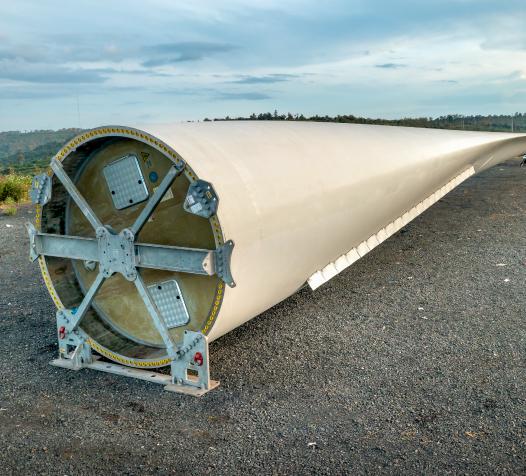
Meeting the Challenges of Machining for Clean Energy.
Meeting the Challenges of Machining for Clean Energy.
New policies, tax incentives, and consumer demand are driving a rapid expansion of the US domestic clean energy manufacturing sector. After decades of depending on products from overseas, entire cleantech supply chains are being reshored. And while much of the focus is on the development of solar and battery supply chains, there are extensive investments in other renewable energy sources that feature more machined components including wind, hydroelectric, and geothermal.
All of this equates to abundant opportunities for machine shops that can reliably produce the components needed for this cleantech revolution. Here are a few things to keep in mind as you consider strategies for moving your shop forward.
Wind power is coming out of hibernation.
Wind power supplies over 10% of our domestic electricity every year, currently our largest source of renewable energy. The domestic supply chain has been established over the past two decades, but dormant in recent years until recent policy changes. Production facilities and new projects are coming back online, so get ready for increased demand of motors, gearboxes, heavy duty bolts, and other machined components.
Full steam ahead on geothermal.
The earth’s heat is available 24/7, and geothermal is an always-on clean energy source for heating, cooling, and power. Emerging geothermal technologies are opening options in areas where traditional hydrothermal is not available, as well as creating new opportunities for in-ground energy storage. Best of all, this emerging field is advancing quickly thanks to the decades of experience and technology developed for oil and gas exploration and production.
More jobs than workers.
The clean manufacturing revolution is projected to create 900,000 new manufacturing jobs in the next decade. Despite recent educational and workforce training initiatives, there are already far more jobs than workers in manufacturing. So, smart shops will need to invest in technology that can dramatically increase output without increasing the demand for skilled labor.
How can you be prepared to take advantage of current opportunities and ready your business for the future? First, invest in the right machining technology. In the rapidly-expanding clean energy manufacturing industry, the right machine tools and processes supercharge machine shops. When you’re adding new equipment, make sure to not just look at increasing your capacity, but augmenting your shop floor with machines that can help you maintain flexibility and increase output while not dramatically increasing the need for new staff in this challenging hiring market.
Second, partner with companies that have charted this path before. This is our not-so-subtle plug for Ellison Technologies (you’re visiting our website; what were you expecting?). We’ve been in business since 1955 and have a long track record in helping clean energy manufacturers achieve their goals. We work with our carefully cultivated list of vendor partners to bring tailored automotive machining technology and turnkey solutions to your shop floor. Ellison Technologies has offices in 16 cities staffed with applications engineers that are ready to help you Make More.
Clean Energy Articles & Customer Stories
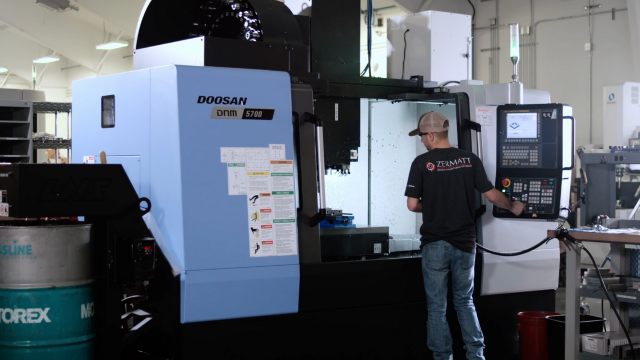
Zermatt Tools
Zermatt Tools
"We put DN Solutions to the test and they passed with flying colors"
-Eric Stieb
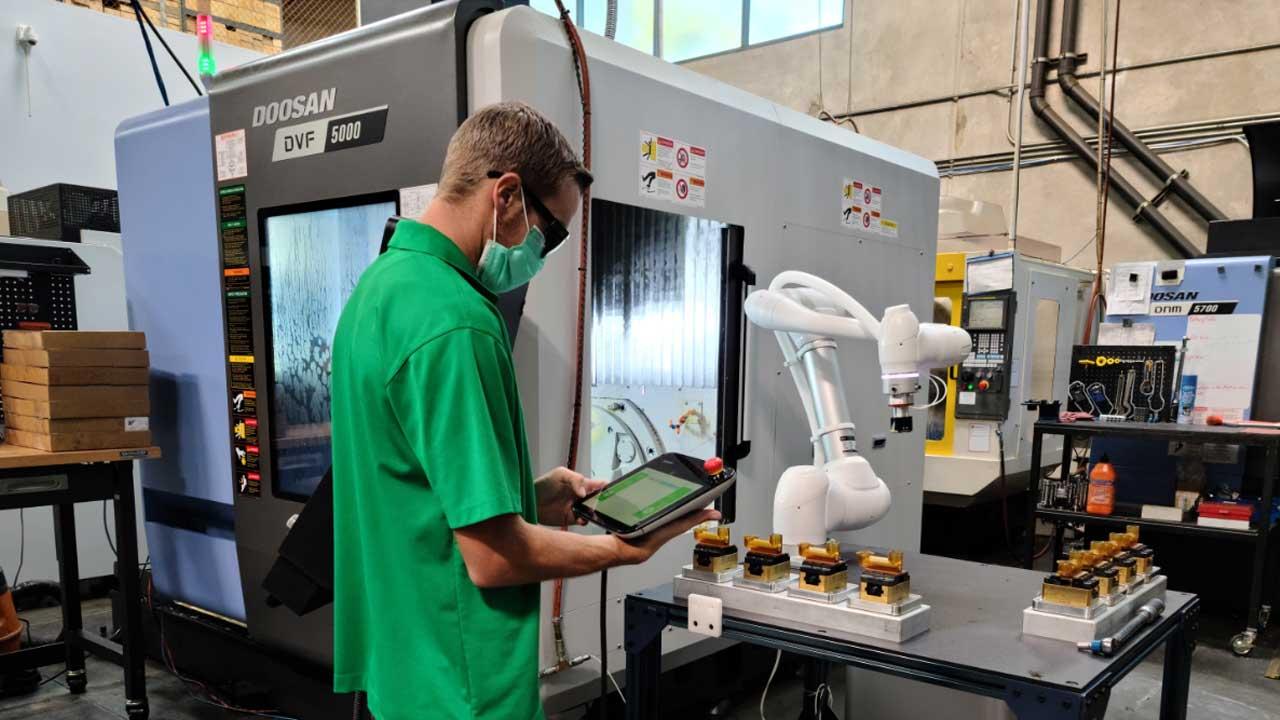
Five Axis Meets Cobot to Deliver Productivity
Five Axis Meets Cobot to Deliver Productivity
"Cycle times are shorter, tool changes are way faster"
-Kyle Christensen
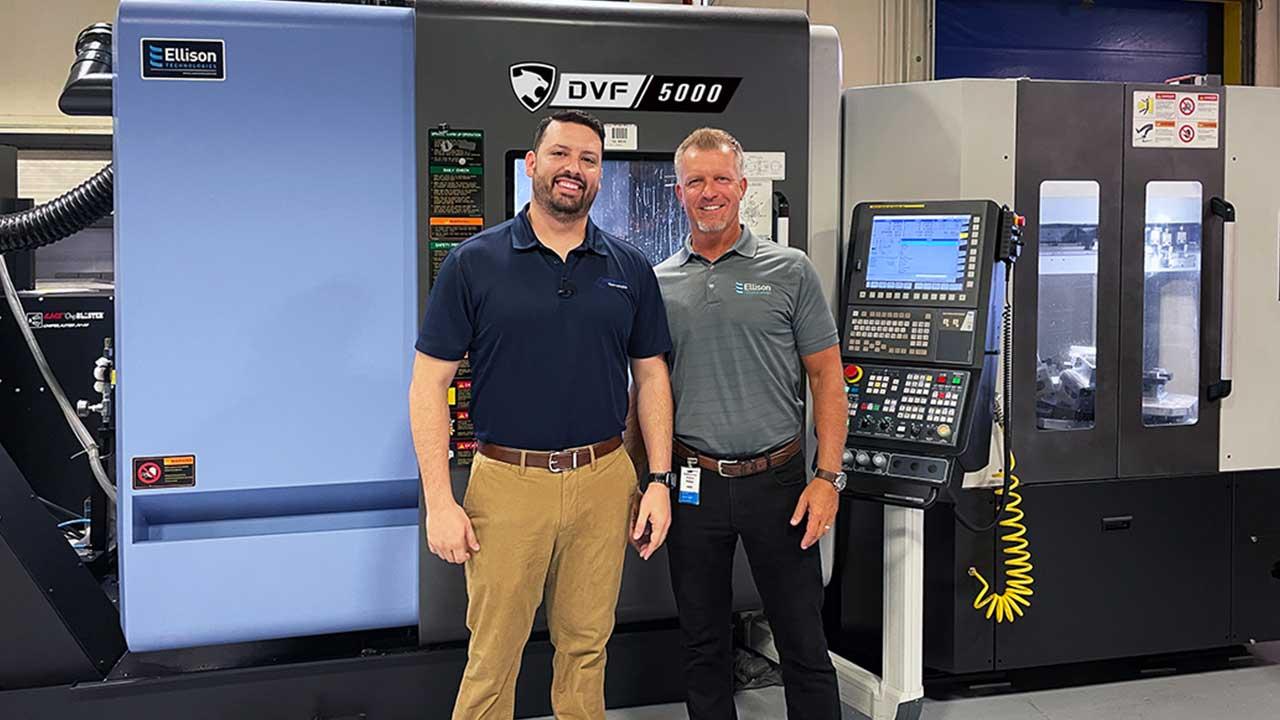
5 Things You Need To Know About the 5-Axis DVF Series from DN Solutions
5 Things You Need To Know About the 5-Axis DVF Series from DN Solutions
Here’s everything you need to know about the DVF Series.
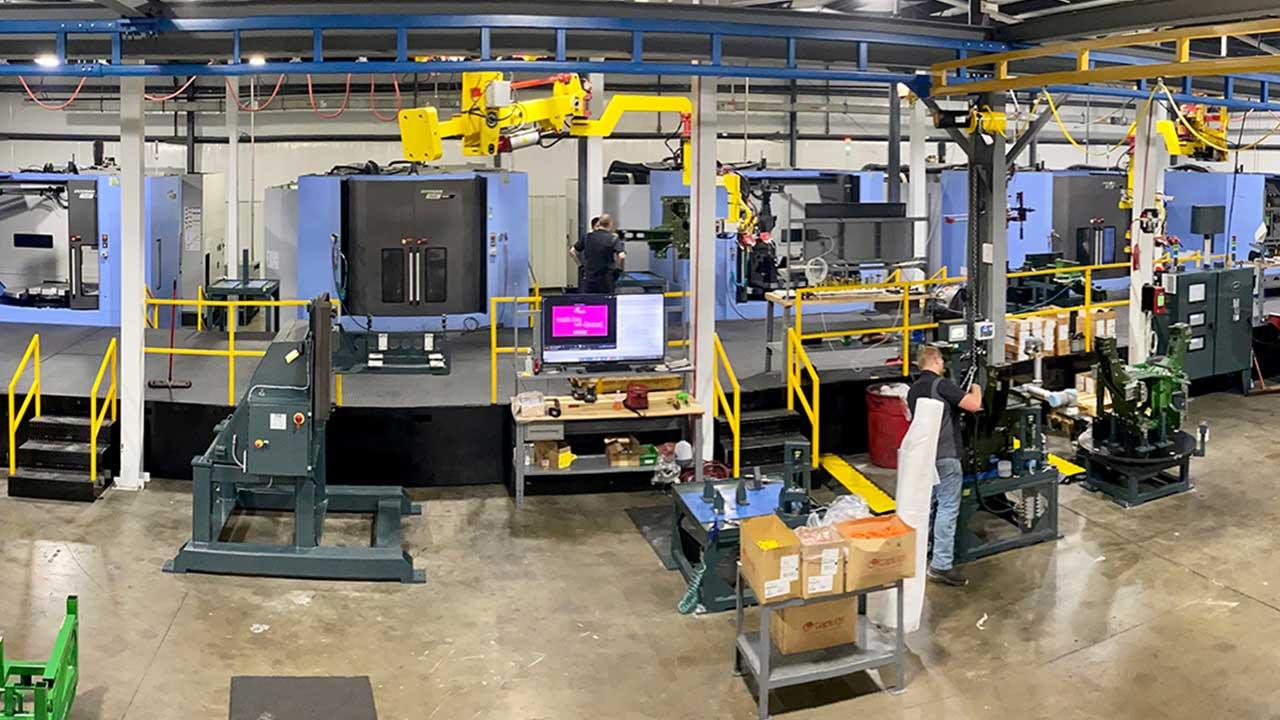
Impact CNC
Impact CNC
Impact CNC won a bid that required five new machining centers to machine mid-frame components.
Learn more about how Ellison can help you succeed in the Clean Energy Industry. Contact Us Today!
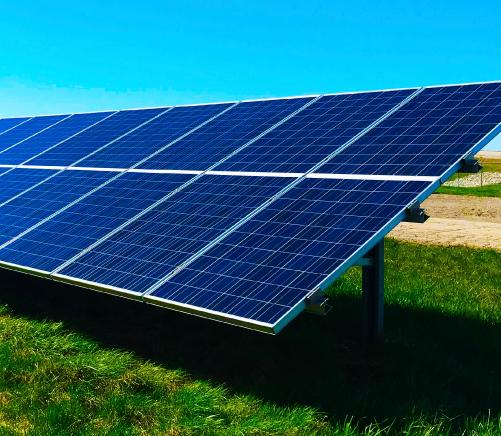
CLEAN ENERGY MACHINING
POSITION YOUR SHOP FOR THE CLEANTECH REVOLUTION
CLEAN ENERGY MACHINING
POSITION YOUR SHOP FOR THE CLEANTECH REVOLUTION
- Get efficiency and accuracy you can count on
- Boost shop-wide capabilities
- Implement top-shelf automation
- Enjoy 24/7 lights out productivity
- Grow revenue and reputation steadily over time
Machines that Make More
The right machine tools make the difference between profit and loss in clean energy machining applications. From our roster of hundreds of different machines, here are some that have consistently made the difference for our customers serving the renewable energy industry.
- Manufacturer: DN Solutions
- Key takeaway: massive lathes for massive parts
- DN Solutions offers several series of vertical turning centers to accommodate a wide range of turning applications. Able to handle parts up to 2 meters (78.7”) in diameter, these rigid machines boast spindles with up to 38,000 Nm (28,000 ft-lb) of torque. When your shop needs muscle, these beasts should be your first call.
- Manufacturer: DN Solutions
- Key takeaway: a VMC series built for productivity
- DNM vertical machining centers come fully-equipped right out of the box, including BIG-PLUS spindles, through spindle coolant, spindle chillers, and dual-screw chip augers. These popular mills are available in a wide range of sizes, with X-axis travels ranging from 520mm (20.5”) to 2,160mm (85.0”).
- Manufacturer: DN Solutions
- Key takeaway: lathes with enhanced rigidity, usability, and accuracy
- Built for heavy machining, the newly designed DNT Series Turning Centers feature box guideways and the most powerful spindle in their class. A redesigned turret body and live tool drive that guarantee powerful and precise machining and exceptional productivity.
- Manufacturer: DN Solutions
- Key takeaway: complex clean energy components have met their match
- With table diameters ranging from 500 - 800mm (19.7” - 31.5”), there is a DVF Series machine for just about every shop. Fast and powerful spindles, large tool magazines, and lights-out automation options are likely to make this family of 5-axis machines the best investment your shop ever makes.
- Manufacturer: DN Solutions
- Key takeaway: compact horizontal mills built for massive metal removal
- Speed and rigidity are the hallmarks of the NHP Series of horizontal machining centers. Pallet sizes range from 400 to 800mm (15.7” to 31.5”), and high-speed spindles, rapid automatic tool changers, and available linear pallet systems deliver reduced cycle times and amazing productivity.
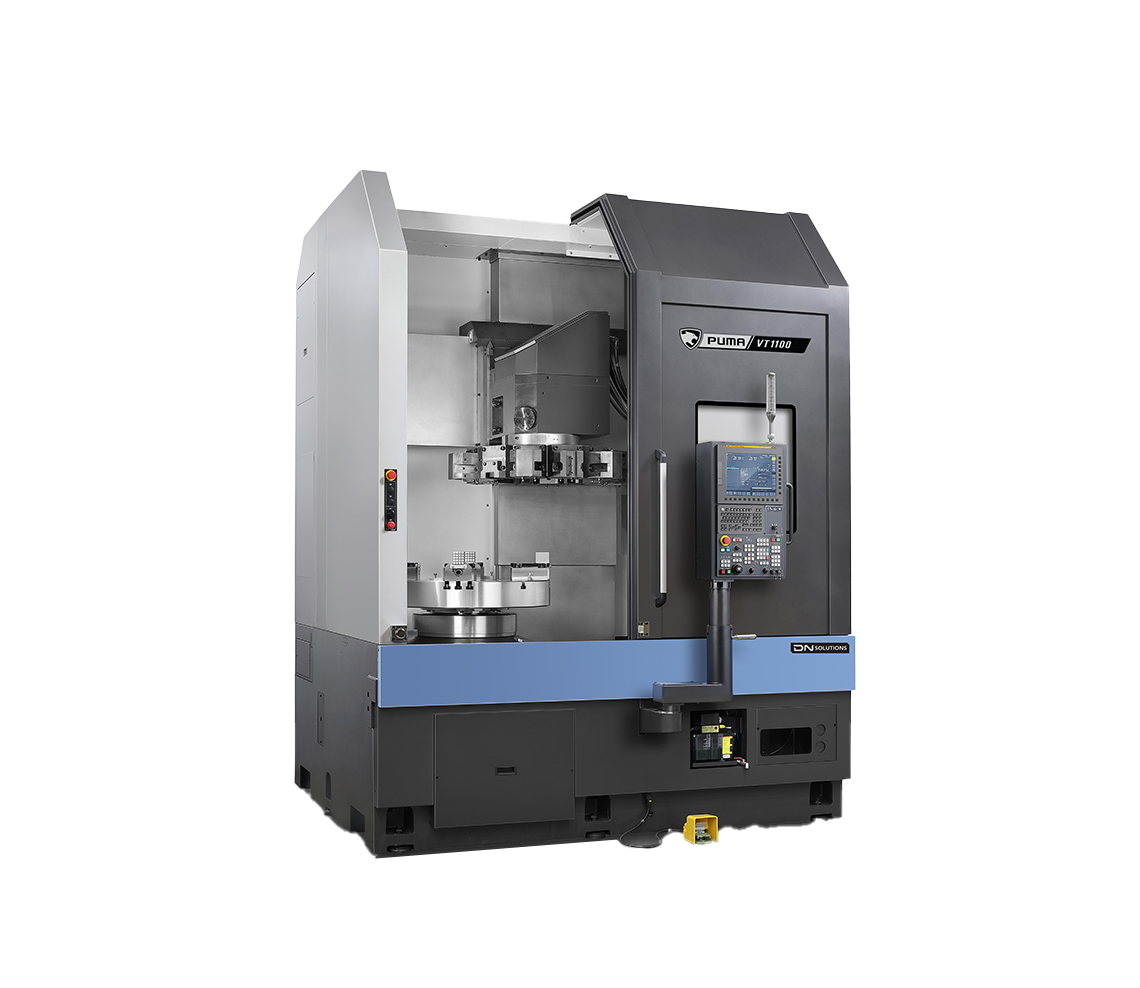
PUMA
Vertical Machining Centers
PUMA
Vertical Machining Centers
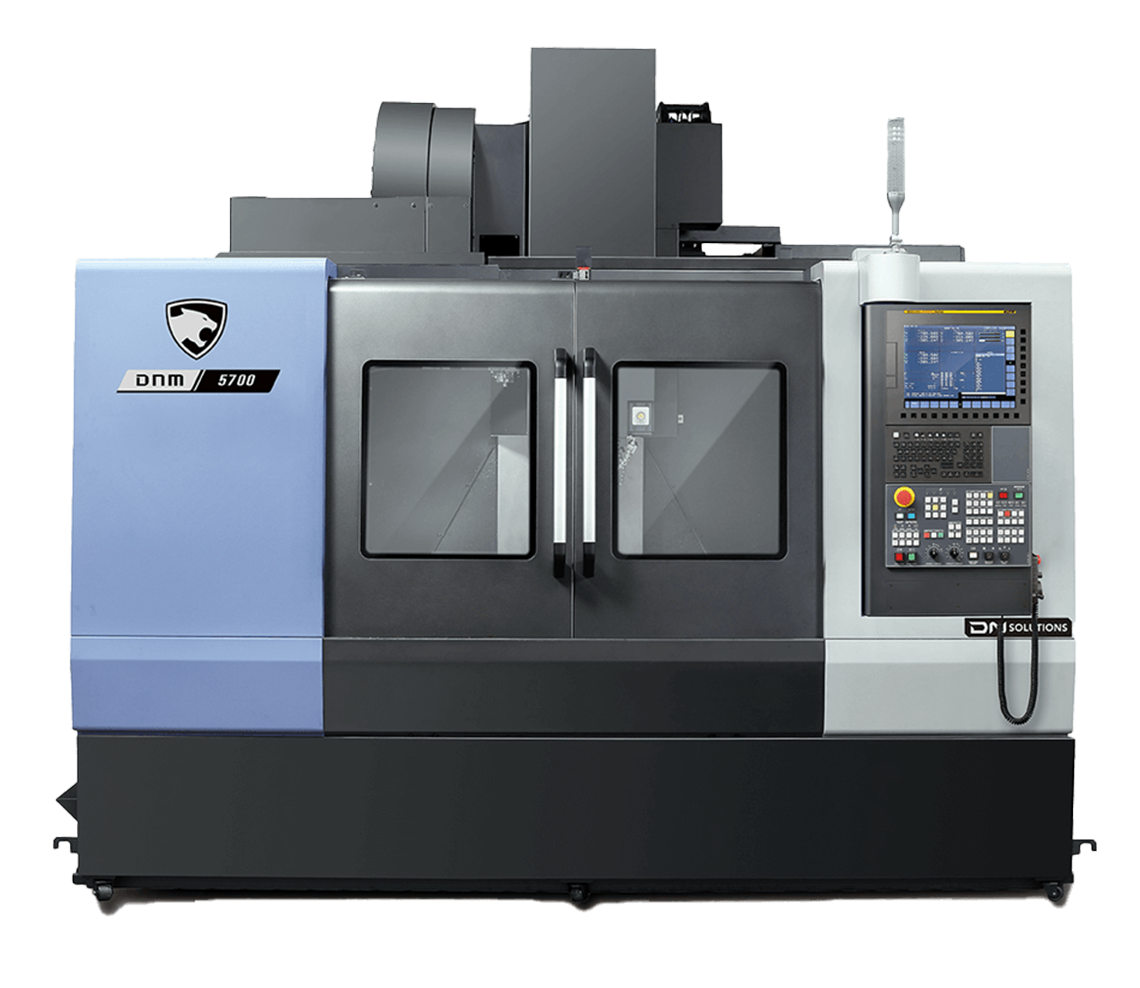
DNM
Vertical Machining Centers
DNM
Vertical Machining Centers
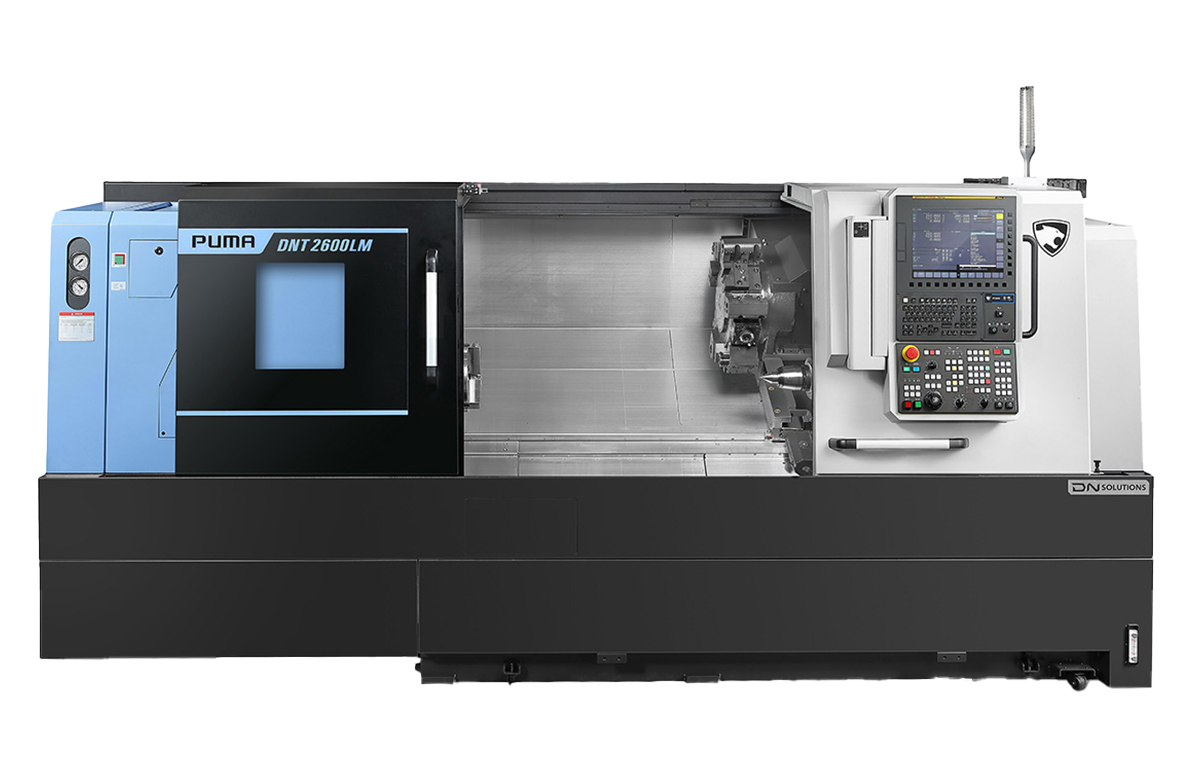
DNT
Horizontal Turning Centers
DNT
Horizontal Turning Centers
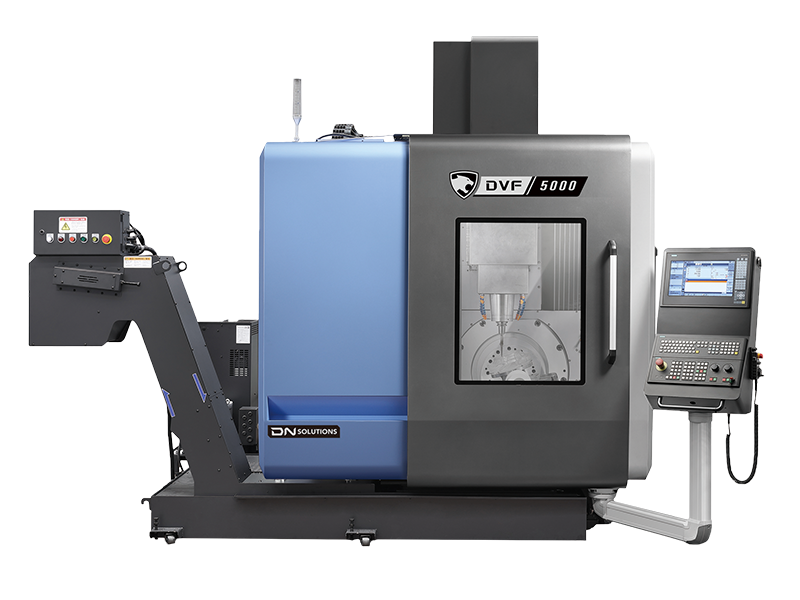
DVF
5-Axis Machining Centers
DVF
5-Axis Machining Centers
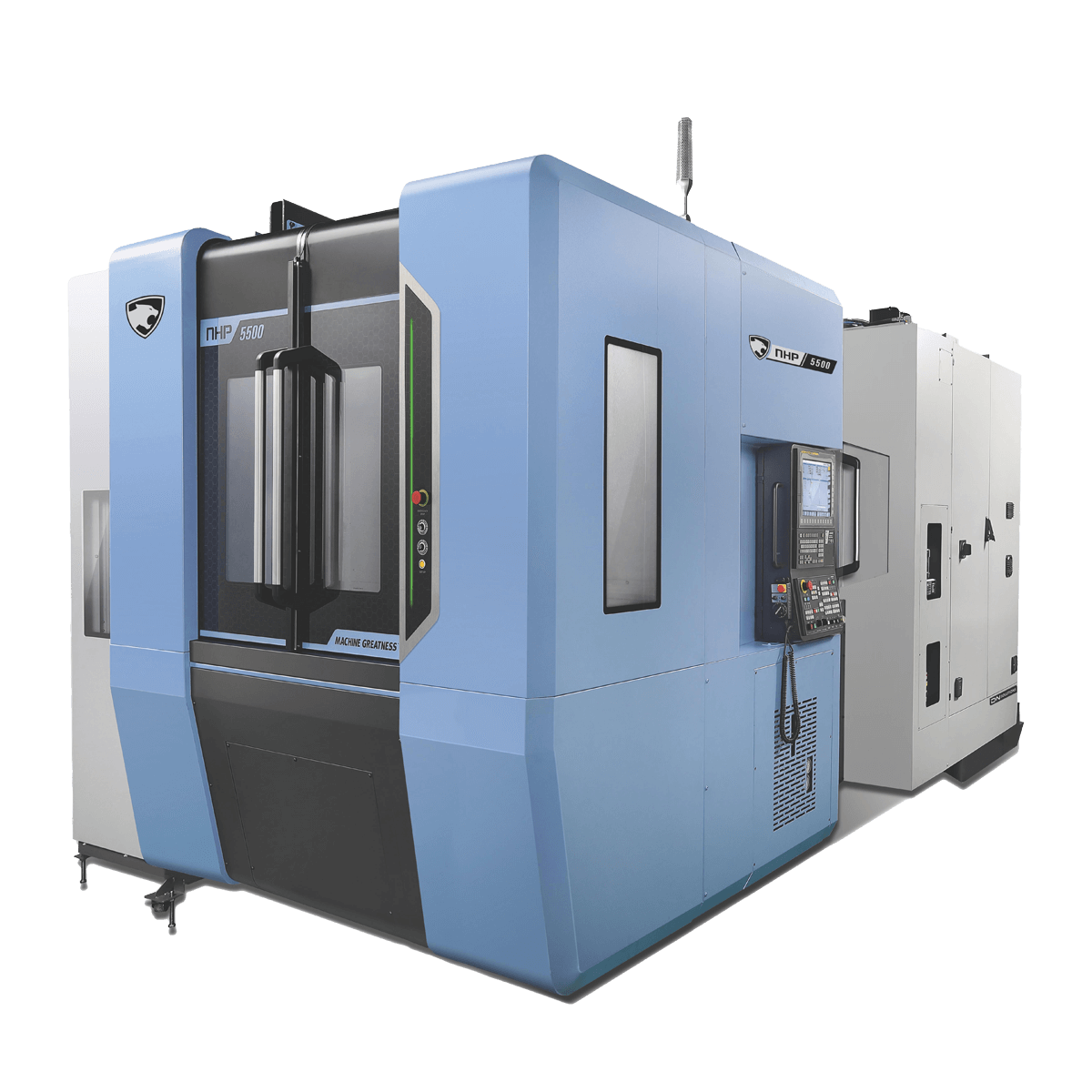