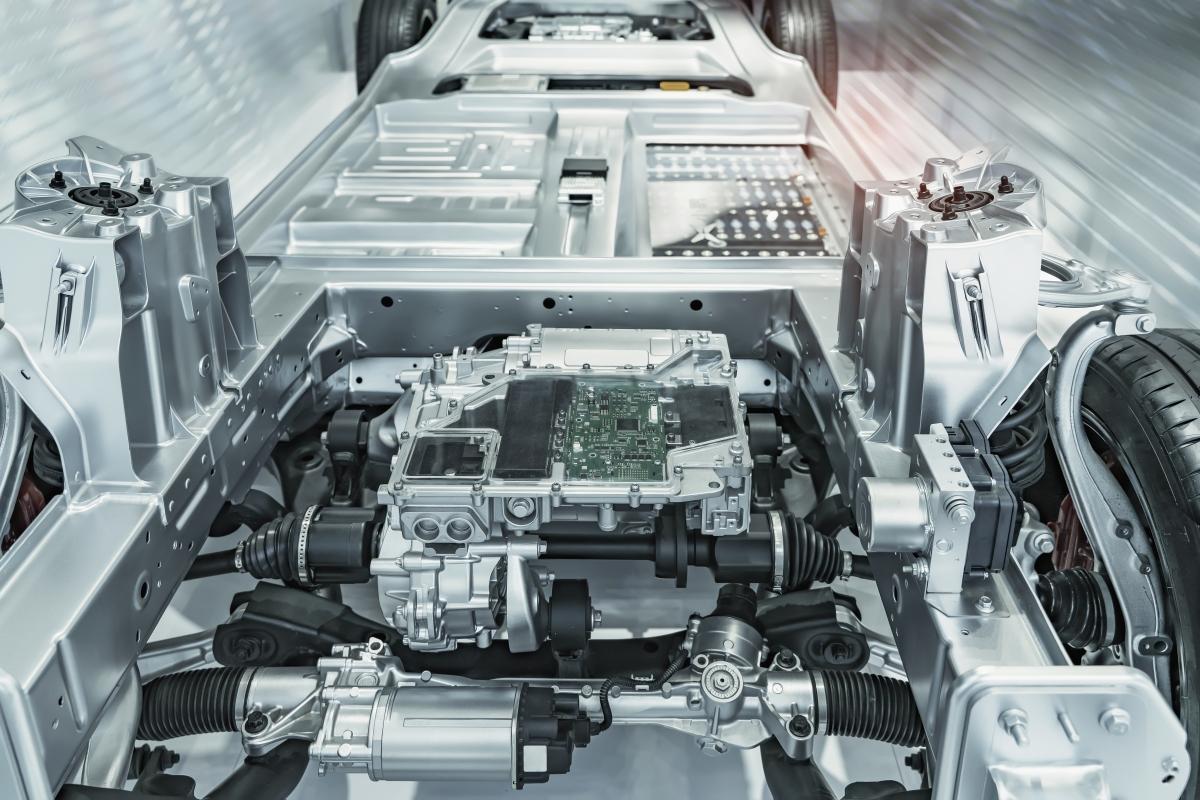
Meeting the Challenges of Automotive Machining.
It’s an interesting time to be in the business of machining automotive components. Unless you’ve been under a rock, you know that OEMs are largely phasing out their internal combustion engine product lines and transitioning to electrical vehicles. Electric vehicles are expected to make up almost 60 percent of new vehicle sales by 2030, so production needs to ramp up fast.
It’s an interesting time to be in the business of machining automotive components. Unless you’ve been under a rock, you know that OEMs are largely phasing out their internal combustion engine product lines and transitioning to electrical vehicles. Electric vehicles are expected to make up almost 60 percent of new vehicle sales by 2030, so production needs to ramp up fast.
We’re going to need electric motors. Lots of electric motors.
While most of today’s EVs have one or two motors, some manufacturers are adding even more for performance and responsiveness. The Lucid Air and Tesla Model S Plaid both feature three motors, and Rivian offers models with four motors. All these motors mean high demand for the machined components that go into them: multiple EV motor housings per unit, precision shafts, bearings and more.
Quiet cars need more precise components.
Which means tight tolerances are getting even tighter. If you haven’t driven an EV yet, one of the first things you’ll notice is how quiet they are. With no internal combustion engine noise to hide the rattles and squeaks, all EV components are going to need to be made to higher standards to keep them quieter. Machined components will need to be more precise, and stampings and moldings will require better dies and molds.
Add lightness (sorry, Colin Chapman).
There is a direct correlation between EV weight and total range. EVs tend to be substantially chonkier than their ICE counterparts, primarily due to the mass of batteries needed. So, EV manufacturers need to shave pounds wherever they can, and are increasingly looking to lighter materials for components previously made from traditional materials. You’ll be hearing lots about composites and magnesium, but don’t count out our old friend aluminum.
That second letter in EV? It stands for “vehicle.”
And like their ICE counterparts, electric vehicles still need machined components for their suspensions, steering systems, drivelines, climate systems, braking systems and more. Body panels and interior components will require new dies machined by 5-axis machining centers. In short: even though the elimination of machining needed for engine and transmission components is significant, there is still a ton of metal cutting needed to produce new electric vehicles.
So how can you be prepared to take advantage of current opportunities and ready your business for the future? First, invest in the right machining technology. In the highly competitive automotive parts manufacturing industry, having the right machine tools is the difference between profit and pain. When you’re adding new equipment, make sure to not just look at increasing your capacity, but augmenting your shop floor with machines that can deliver the high precision parts and maintain the extreme uptime that high volume automotive part production demands.
Second, partner with companies that have driven this road before. This is our not-so-subtle plug for Ellison Technologies (you’re visiting our website; what were you expecting?). We’ve been in business since 1955 and have a long track record in the automotive industry. We work with our carefully cultivated list of vendor partners to bring tailored automotive machining technology and turnkey solutions to your shop floor. Ellison Technologies has offices in 16 cities staffed with applications engineers that are ready to help you Make More.
Automotive Articles & Customer Stories
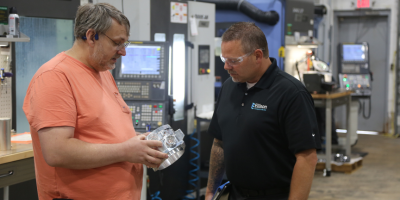
Quali-Mac
Quali-Mac
"With 5-axis, we can machine multiple faces in one setup."
-Brady Bjorgaard
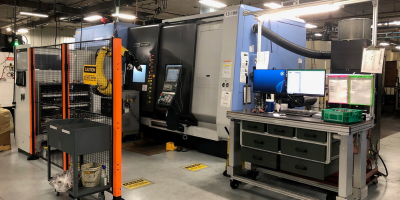
ZF Mico
ZF Mico
"We were looking for something that could complete the parts on one machine"
-Aaron Schlumpberger
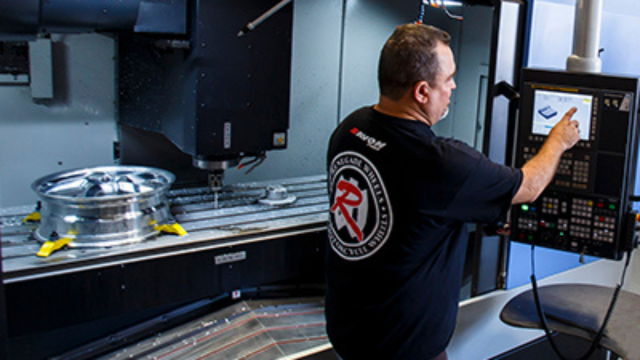
Renegade Wheels
Renegade Wheels
"[We are] reducing time and costs spent polishing each wheel"
-Chuck Frederick
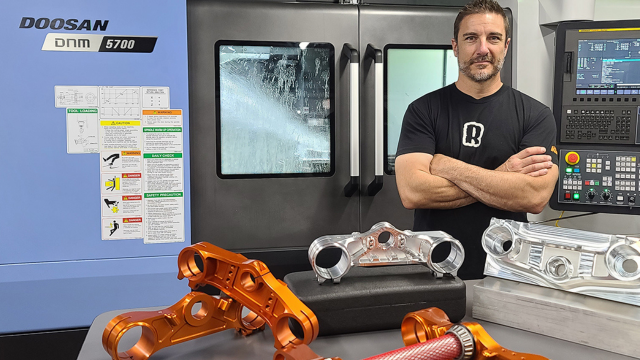
Rottweiler Performance
Rottweiler Performance
"We couldn’t hold these tolerances before"
-Chris Parker
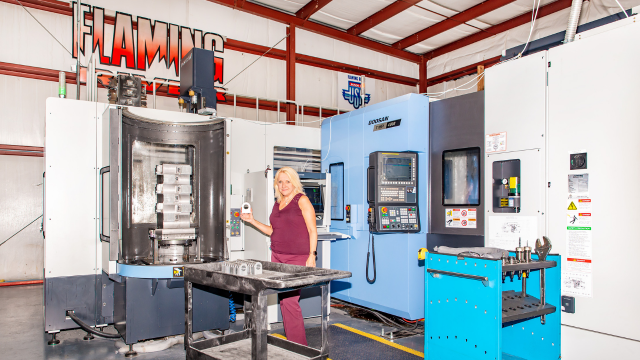
Flaming River
Flaming River
"The new machines, with more power and beefier spindles, run parts faster"
-Jeanette Ladina
Automotive applications, say hello to automotive solutions
At Ellison Technologies, we offer a wide range of technology and solutions that can produce automotive components with precision and efficiency, regardless of the production volume or tolerances required. Our portfolio is comprehensive, providing you with everything you could possibly need.
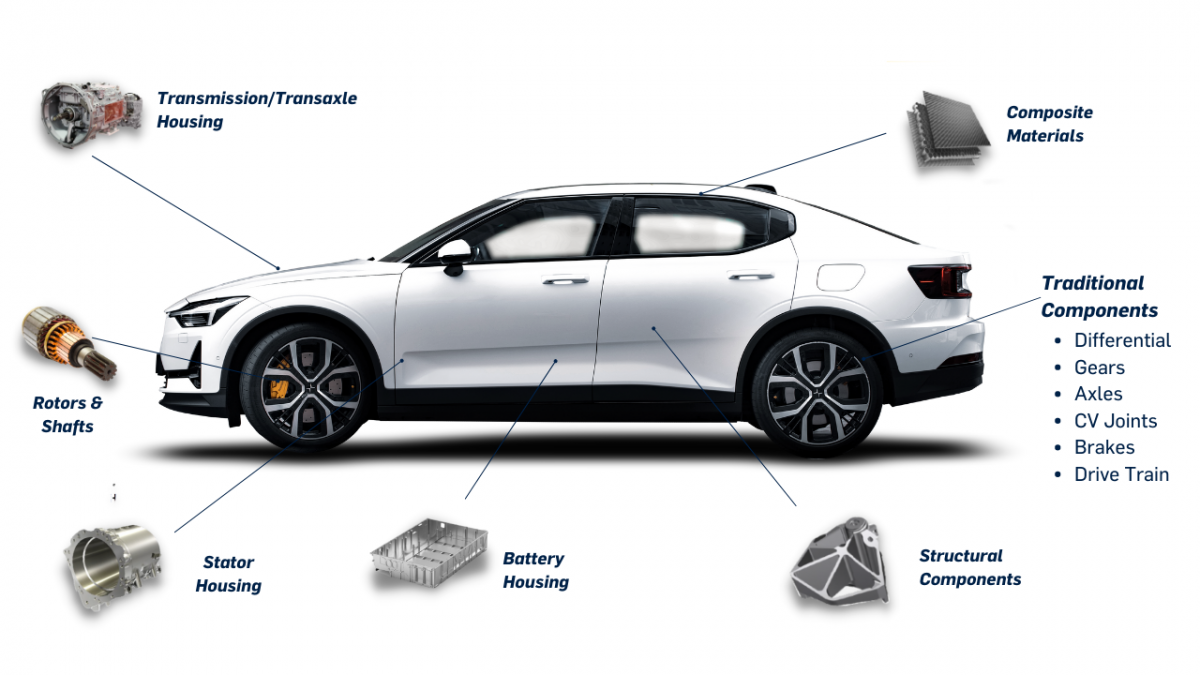
Machines that Make More
The right machine tools make every automotive parts machining job easier. From our roster of hundreds of different machines, here are seven that have consistently made the difference for our customers serving the automotive industry.
- Manufacturer: DN Solutions
- Key takeaway: 24/7 automated high volume production
- The PUMA TW features parallel twin spindles and twin live tool turrets, making it ideal for production automotive jobs like ring gear and clutch boss applications. The gantry loader maximizes cutting time, and work stockers set you up for three shifts of unmanned production.
- Manufacturer: DN Solutions
- Key takeaway: Two spindles in one VMC = maximum production in minimal footprint
- A lot of shops use two identical vertical machining centers and two operators to produce the exact same part. Designed for mid to high volume production runs, the DMP 500/2SP frees up floor space and operator time. Twin spindles, twin ATCs, twin turrets and an adjustable W-axis will instantly double your production.
- Manufacturer: DN Solutions
- Key takeaway: Compact high-performance machines with automation options
- Available in pallet sizes from 400 to 800 mm (15.7” to 31.5”) and with spindles from 6,000 to 20,000 RPM, the NHP Series is built to tackle a wide range of automotive applications. Add on a larger matrix tool magazine, compact rotary pallet system, or an expandable linear pallet system for lights-out machining.
- Manufacturer: DN Solutions
- Key takeaway: Best-in-class heavy duty boxway turning centers
- If you turn parts in tough-to-machine materials, there is a PUMA 2600 with your name on it. Rigid machine beds and powerful spindles are just the start. Add on sub-spindles, live tools, and a Y-axis and the PUMA 2600 will machine complex automotive parts in a single setup.
- Manufacturer: DN Solutions
- Key takeaway: Compact VTC designed for production applications
- With a compact footprint of only 58” x 82”, PUMA V400 vertical turning centers are built with boxways for long shifts filled with heavy duty cutting. Productivity-enhancing options, including a second spindle and 12-station live tooling turret, are available for even shorter cycle times.
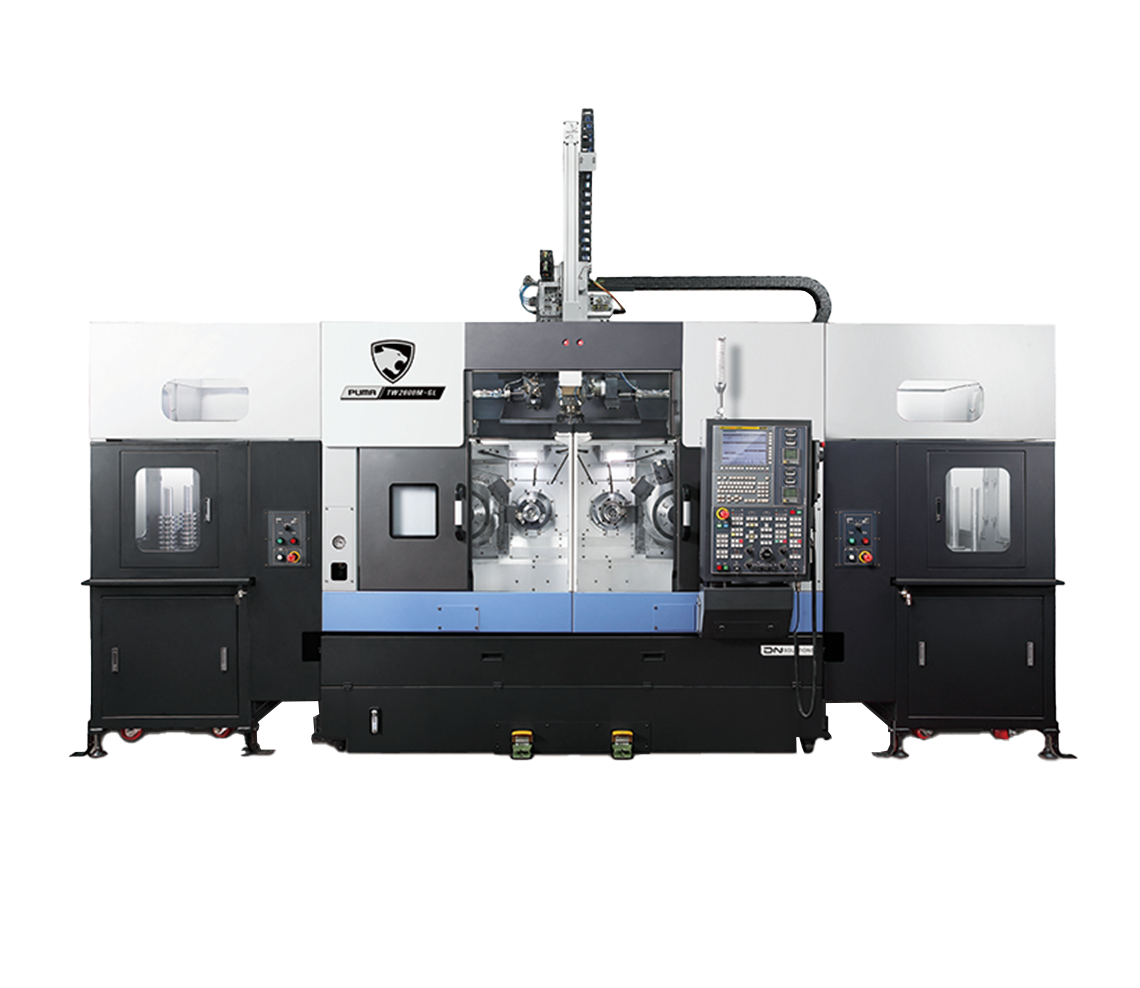
PUMA TW2100/M
Twin Spindle Horizontal Turning Center with Gantry Loader
PUMA TW2100/M
Twin Spindle Horizontal Turning Center with Gantry Loader
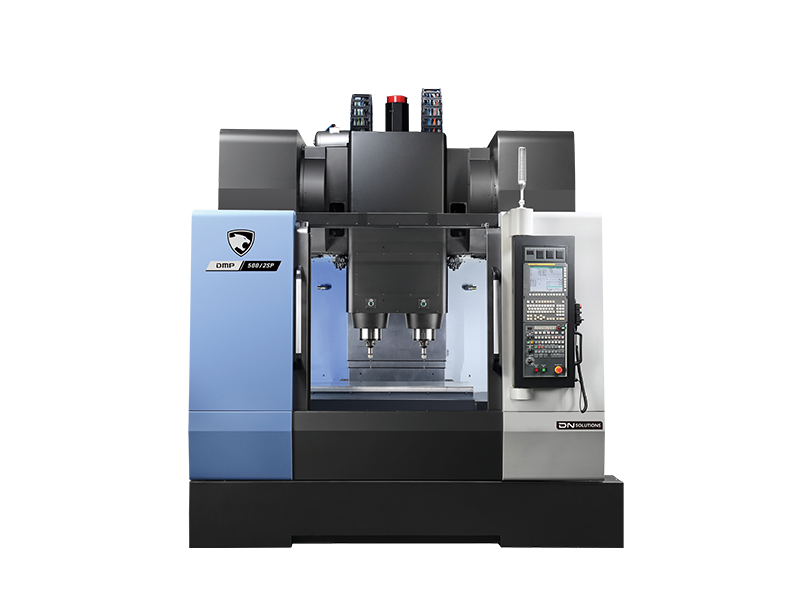
DMP 500/2SP
Twin Spindle Vertical Machining Centers
DMP 500/2SP
Twin Spindle Vertical Machining Centers

NHP Series
Horizontal Machining Centers
NHP Series
Horizontal Machining Centers
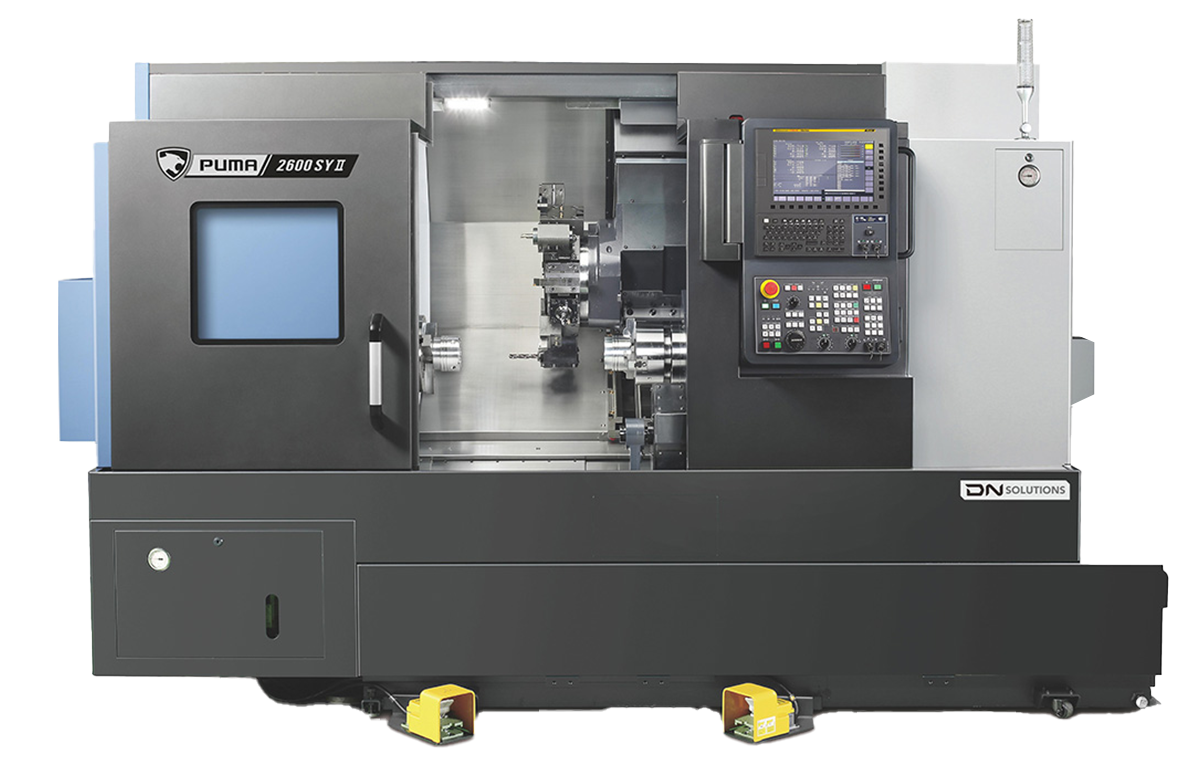
PUMA 2600
Horizontal Turning Centers
PUMA 2600
Horizontal Turning Centers
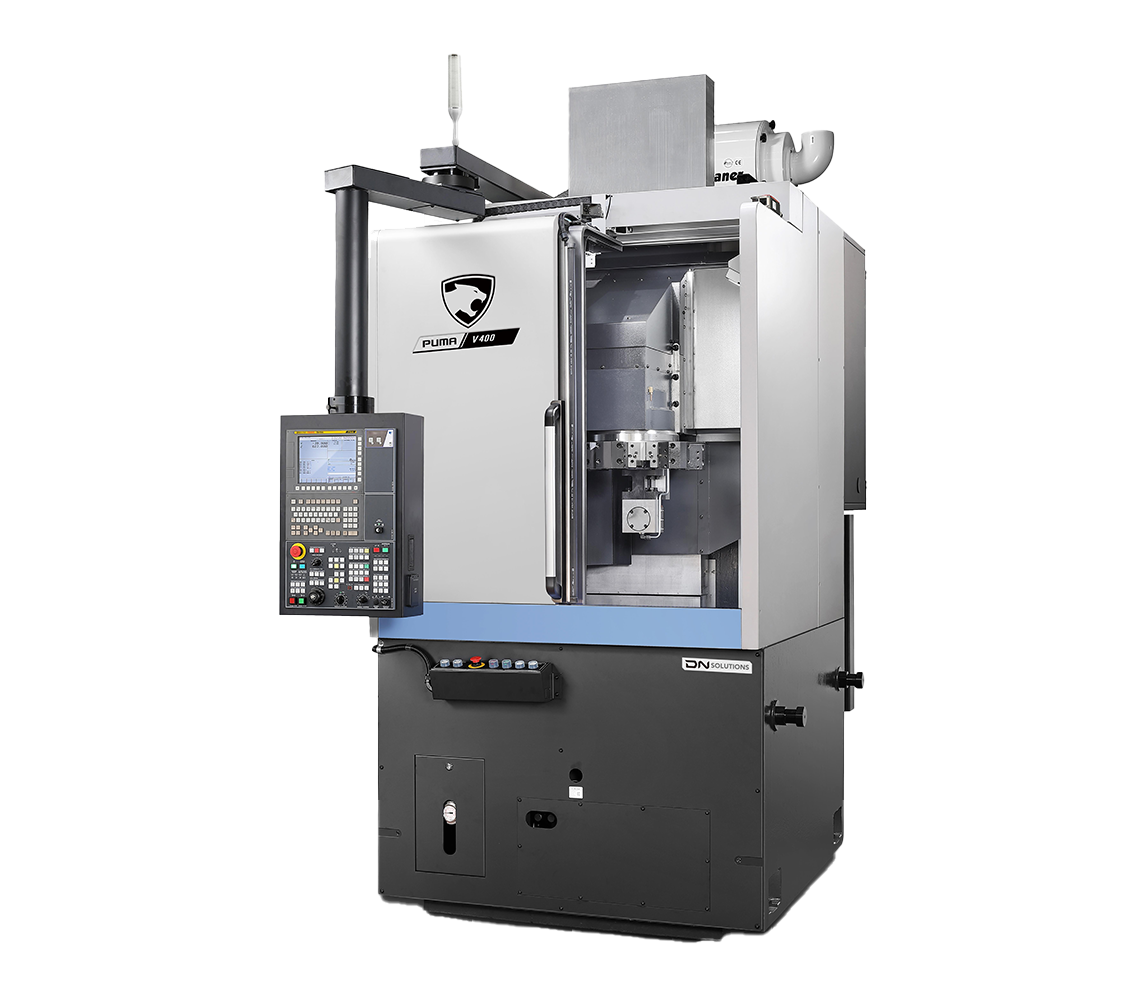
PUMA V400
Vertical Turning Centers
PUMA V400
Vertical Turning Centers
- Manufacturer: HELLER
- Key takeaway: Robust 5-axis machining centers for complex parts
- The HF Series is built to work in production machining environments, and there are zero compromises on build quality and machine rigidity. These 5-axis horizontal machines feature ball screw drives and rapid traverse rates up to 90 m/min (3,543 IPM), giving you both reliability and speed for your most demanding applications.
- Manufacturer: HELLER
- Key takeaway: Powerful milling and turning combined on one machine
- The C Series combines a spindle unit with a swivel or tilting head with a DDT (Direct Drive Turning) rotary table for universal 5-axis milling and turning in a single machine. The entire machine, including automation options, has been designed for production of complex parts where precision and cost performance per piece are paramount.
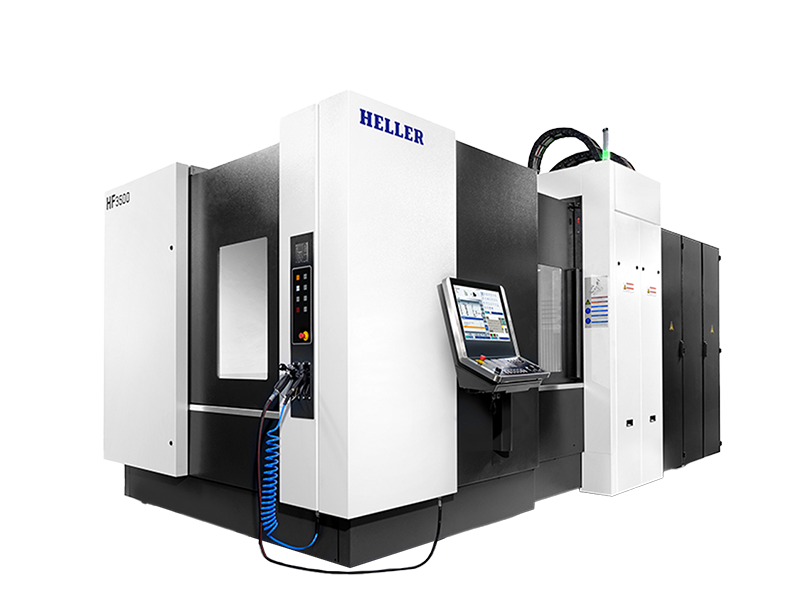
HF Series
5-axis Horizontal Machining Centers
HF Series
5-axis Horizontal Machining Centers
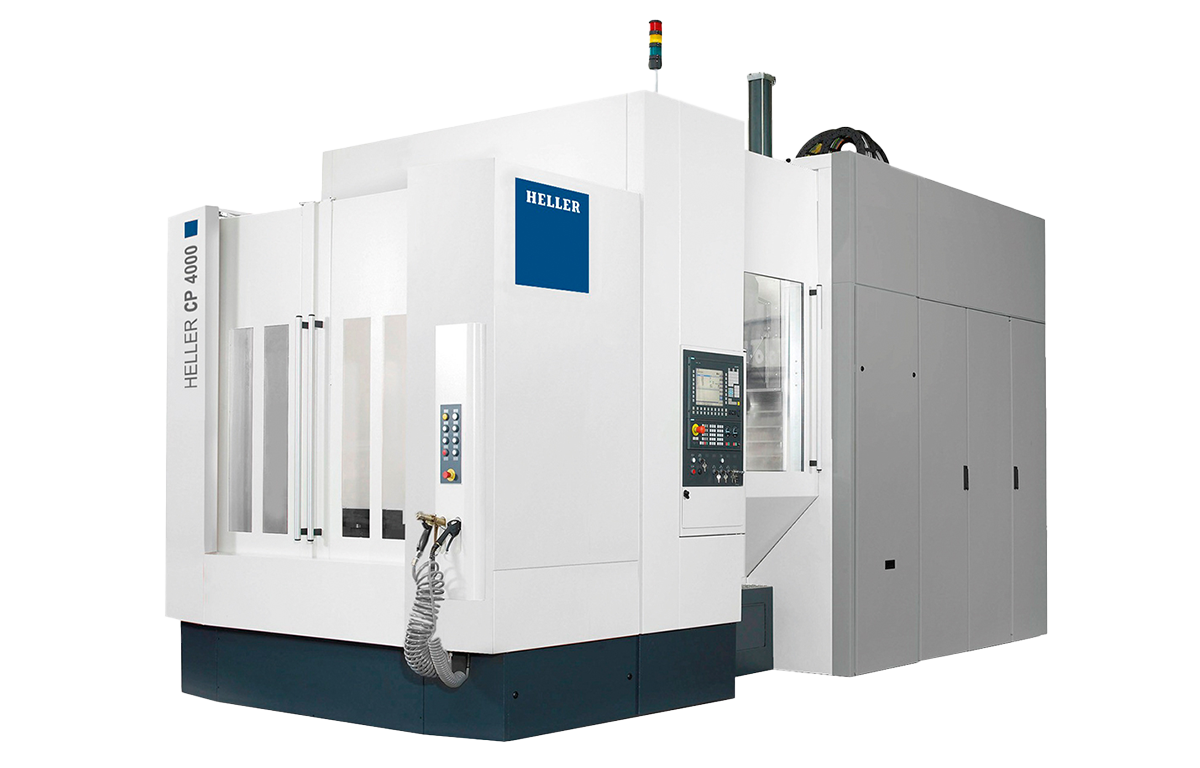
C Series
5-Axis Machining Centers with Turning
C Series
5-Axis Machining Centers with Turning
Learn more about how Ellison can help you succeed in the Automotive Industry. Contact Us Today!
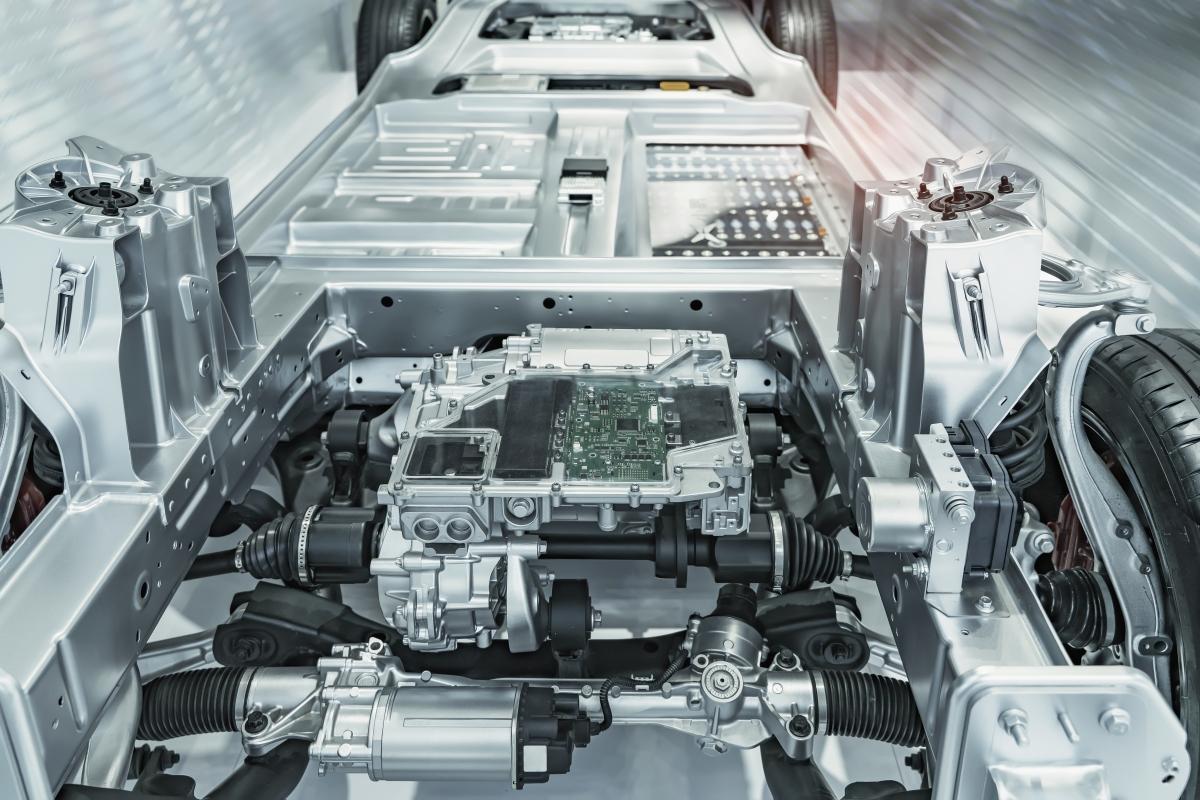
AUTOMOTIVE MACHINING
ACCELERATE YOUR PART PRODUCTION—AND BOOST REPUTATION AND REVENUE
AUTOMOTIVE MACHINING
ACCELERATE YOUR PART PRODUCTION—AND BOOST REPUTATION AND REVENUE
- Increase efficiency
- Pinpoint part accuracy
- Level up shop capabilities
- Take advantage of automotive automation
- Get 24/7 lights out productivity
- Watch revenue floor it and never look back