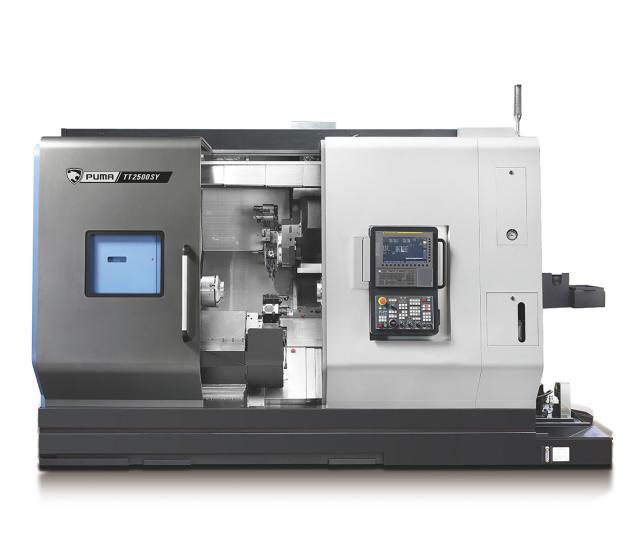
PUMA TT Series
The PUMA TT Series is designed for superior surface finishes and long-term high accuracy. Twin turrets and twin spindles are a great high productivity solution, especially for handling small-sized & complex parts for mass production. Multi-tasking capabilities increase productivity by reducing work in process.
-
Rapid Traverse X-axis20 m/min (787 in/min)
-
Rapid Traverse Y-axis7.5 m/min (295 in/min)
-
Rapid Traverse Z-axis24 m/min (945 in/min)
-
Rapid Traverse C-axis200 rpm
-
Travel Distance X1-axis255 mm (10 in)
-
Travel Distance Z1-axis800 mm (31.5 in)
-
Travel Distance X2-axis190 mm (7.5 in)
-
Travel Distance Z2-axis900 mm (35.4 in)
-
Travel Distance Y-axis120±60 mm (4.7±2.4 in)
-
ShankBMT-65
-
Turret Stations12/Turret
-
Boring Bar Diameter⌀40 mm (1.5 in)
-
Rotary Tool Speed5000 rpm
-
Rotary Tool Power7.5 kW (10 Hp)
-
Rotary Tool Torque95.5 Nm (70 ft-lbs)
-
Weight12700 kg (27990 lbs.)
-
Length4150 mm (163 in.)
-
Height2480 mm (98 in.)
-
Width2210 mm (87 in.)
-
Max Turning Diameter (Upper Turret)⌀390 mm (15.4 in)
-
Max Turning Diameter (Lower Turret)⌀300 mm (11.8 in)
-
Max Turning Length350 mm (13.8 in)
-
Through Hole Diameter (Left Spindle)⌀82 mm (3.2 in)
-
Through Hole Diameter (Right Spindle)⌀75 mm (2.9 in)
-
Power26 kW (35 Hp)
-
Torque433 Nm (319 ft-lbs)
-
Chuck Size10 in
-
Speed3500 rpm
PUMA TT Series:
Dual-Turret, Multi-Axis Turning Centers
The PUMA TT Series features dual-turret technology for simultaneous machining, maximizing productivity with high-speed multi-axis turning solutions.
- PUMA TT1800SY: Dual-spindle, dual-turret machine for increased throughput in high-volume production environments.
- PUMA TT2100SYYB: Enhanced with additional milling and turning capabilities for more demanding applications.
Additional Features and Benefits
- Dual-Turret Design for Simultaneous Machining: Increases efficiency and reduces cycle times.
- Advanced Control Systems: Offer precise synchronization between spindles and turrets for seamless operation.
- Optimized for High-Volume Production: Ideal for automotive and other industries demanding rapid part turnover.
Powerful Twin-Turret Performance for Complex Machining
The PUMA TT2500SY is engineered for high-volume, high-precision turning and milling applications. With its twin-turret architecture and upper Y-axis capability, it completes multi-operation parts in a single setup. This allows for significant reductions in cycle time, tool changes, and handling errors. It's a production-ready multitasking solution for manufacturers focused on throughput and accuracy.
Integrated Y-Axis and C-Axis for Complete Flexibility
The upper turret features a ±2.36" Y-axis, allowing off-center operations like cross-drilling, slotting, and milling. Both spindles are equipped with full C-axis contouring control, enabling interpolation and synchronized motion. This multi-axis flexibility gives you the power to machine intricate features on multiple sides of a part—without needing to move it to another machine.
High-Speed Live Tooling Across Both Turrets
Each of the machine’s 12-station BMT65 turrets supports live tooling at every station, driven by 10 HP motors capable of up to 5,000 RPM. This setup allows simultaneous turning and milling on both spindles, and with live tools at all stations, tooling versatility and efficiency are maximized. Indexing is fast and servo-driven, further reducing non-cutting time between operations.
Heavy-Duty Construction for Rigid, Repeatable Cuts
The TT2500SY is built on a 45° slant-bed Meehanite® casting for superior vibration damping and thermal stability. Large linear roller guides ensure rigidity and rapid axis movements. Ball screws are supported and cooled to reduce thermal expansion during extended cutting cycles, keeping the machine within spec even on long runs or with hard materials.
Automation-Ready with Built-In Productivity Enhancers
This machine comes standard with a programmable parts catcher, parts conveyor, twin tool setters (one per turret), and a coolant system optimized for chip management. These features allow the TT2500SY to run unattended for long periods—ideal for high-mix, high-volume production environments. The optional high-pressure coolant system (up to 1,000 PSI) further enhances chip control and tool life.
Smart CNC Control for Advanced Machining
Powered by the FANUC 0i-Plus control with Easy Operation Package (EOP), the machine supports polar interpolation, helical milling, synchronized cutting, and sub-spindle part transfer. The swiveling control panel and conversational interface reduce training time and make the machine accessible to shops with varying levels of programming experience.
FAQ Section
What applications is the PUMA TT2500SY best suited for?
The PUMA TT2500SY is designed for multi-tasking environments where complex parts require multiple operations—turning, milling, drilling, and tapping—across multiple faces. It is particularly valuable in industries like aerospace, automotive, medical device manufacturing, and oil & gas where tight tolerances and high surface finishes are essential. Its dual turrets and twin spindles allow simultaneous machining, effectively reducing setup and cycle times.
How does the Y-axis on the TT2500SY enhance part machining?
The Y-axis on the upper turret adds ±2.36" of off-center travel, enabling complex milling and drilling operations above and below the centerline. This eliminates the need for secondary setups or specialized tooling. Applications include machining cross-holes, flats, slots, and keyways with high precision. The double-slide wedge design maintains rigidity, even under demanding cutting loads, ensuring consistent part quality.
What makes the TT2500SY ideal for lights-out manufacturing?
The TT2500SY includes several automation-enabling features: a programmable part unloader with conveyor, twin automatic tool setters, barfeed interface, and tool load monitoring. These systems allow the machine to operate with minimal operator intervention, making it ideal for high-volume, unattended machining. The right spindle's coolant-flushed part ejector ensures reliable part removal even during long runs.
Can the TT2500SY handle high-pressure coolant?
Yes, the TT2500SY supports optional coolant systems up to 1,000 PSI. High-pressure coolant enhances chip evacuation, improves surface finish, and extends tool life—especially during deep-hole drilling or high-speed milling operations. The base machine comes standard with 65 PSI coolant and can be upgraded to 145 PSI or 1,000 PSI depending on application needs.
How accurate is the machine for multi-axis contouring?
Equipped with C-axis functionality on both spindles and FANUC 0i-Plus control, the TT2500SY offers full contouring and interpolation capabilities. The machine maintains positioning accuracy of ±0.0167° and repeatability of ±0.006°, supporting high-precision contouring, threading, and synchronized milling operations across spindles.