Do you find yourself turning down business because you don’t have the resources to turn the job around in the customer’s time frame? Is unproductive downtime eating into your profit margin? Are you having trouble finding experienced machinists?
You’re not alone.
Many machining and fabrication shops are finding themselves locked into the need to make more precision parts faster with fewer resources. Quite the conundrum. Fortunately, there’s a solution. By matching the power and flexibility of the DN Solutions (formerly Doosan Machine Tools) DVF Series 5-axis vertical machining centers with automation, you can increase throughput while reducing the need for human intervention.
The DN Solutions (formerly Doosan Machine Tools) DVF Series is fully packaged to manage diverse 5-sided or simultaneous 5-axis applications. Let’s take a quick look at the lineup and the most popular automation options for each machine.
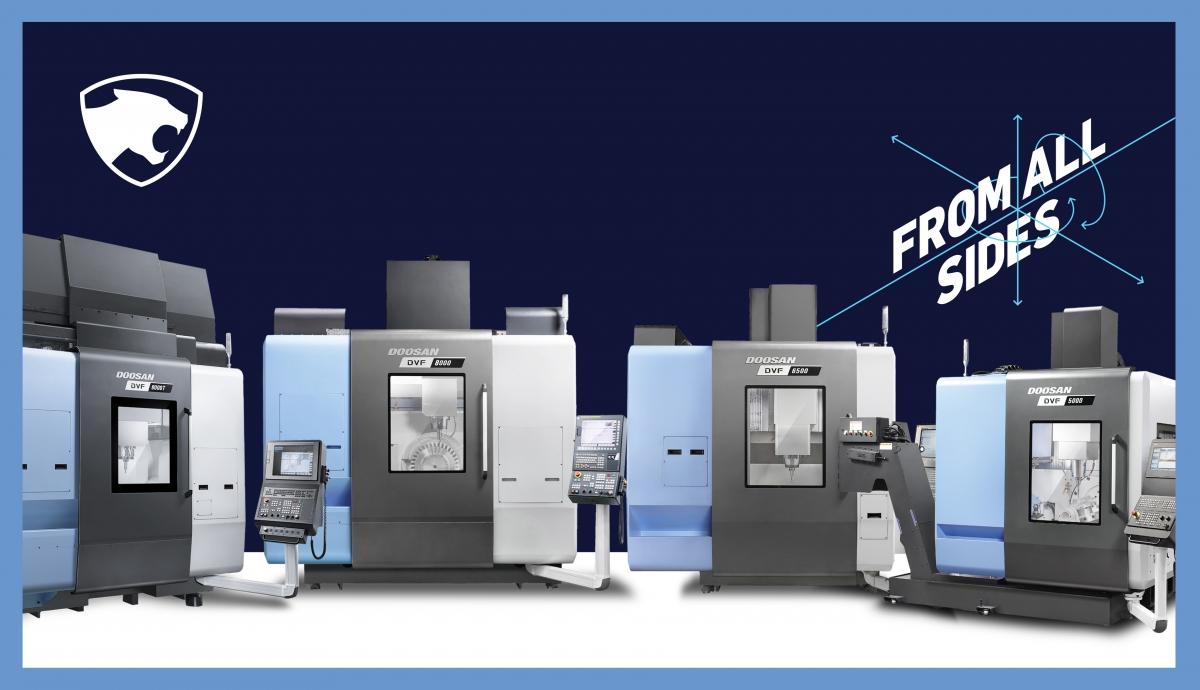
DVF 5000
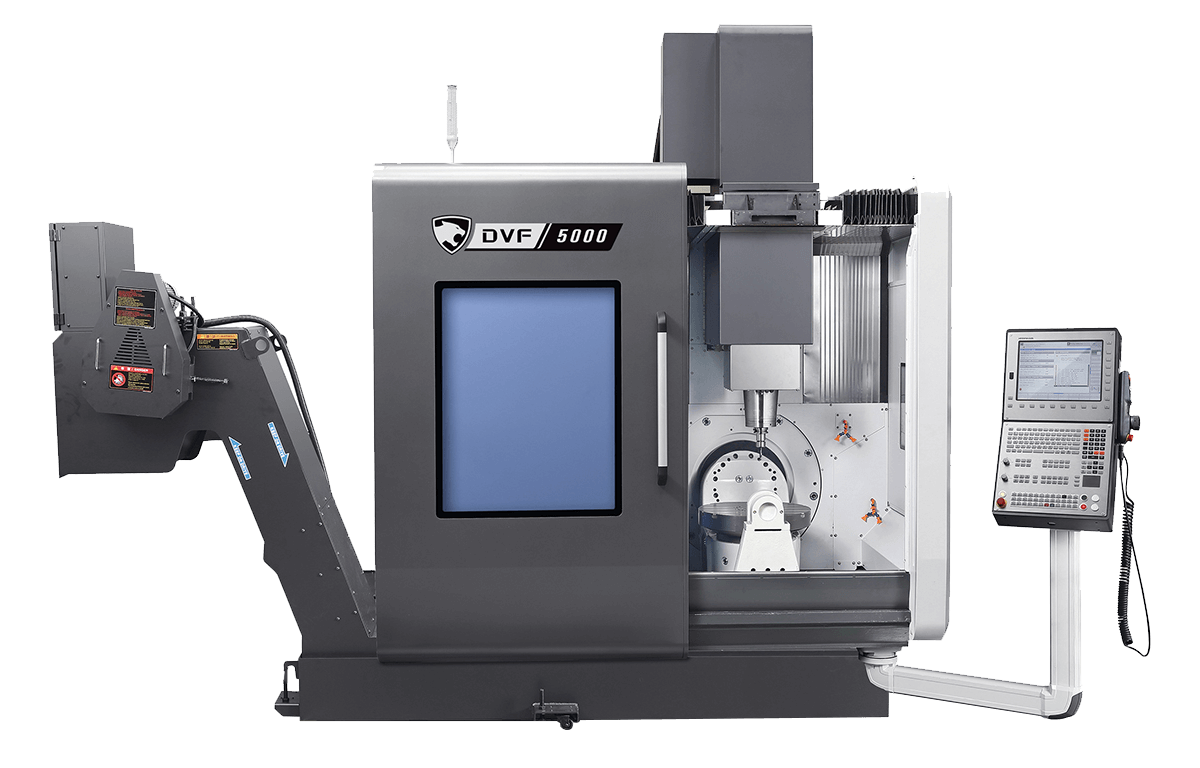
It all began with the DN Solutions (formerly Doosan Machine Tools) DVF 5000, which was designed to cut the most complex shapes with just one setup. It comes standard with an 18,000 r/min integral Big Plus 40 taper spindle. A FANUC 31iB5 CNC controller makes full 5-axis simultaneous control possible, giving complete contouring capabilities. It’s the most compact member of the DVF family with a 500mm rotary table.
Automation Partner: The most popular pairing here is the eight-pallet Automatic Work Changer (AWC) that sits to the right of the machine (facing it). Since the DVF 5000 rotary axes are a cantilevered B and C configuration, pallets move in and out thru an automatic sliding door on the right side, allowing the operator full access to the front of the machine and CNC controller.
Shops that are interested in this setup usually want to put enough raw stock on the pallets to get through the night (perhaps adding a virtual shift) and come into the shop in the morning with completed parts waiting for them.
Another scenario is a high-mix, low-volume environment where the AWC needs to be ready to respond to a last-minute customer demand. To facilitate this, the cell controller for the AWC is capable of handling basic functions like simple scheduling, displaying status information and the ability to break a programmed routine (manually override an automated schedule).
The AWC is also available in pallet configurations of 4, 6, 10 and 12. If you want to build up, not out, a multi-level AWC can be purchased for the DVF 5000. It comes with 40 pallets (250 x 250 only).
DVF 6500
The slightly larger DN Solutions (formerly Doosan Machine Tools) DVF 6500 has an integrated 25.6" (650mm) diameter A- over C-axis rotary table. The C-axis is driven by a highly rigid roller gear cam and the A-axis is driven by tandem roller gear cams for maximum stiffness and rigidity. The DVF 6500 also has many of the same features of the DVF 5000.
Automation Partner: The DVF 6500 is commonly teamed up with a Rotary Pallet System (RPS) with 7 pallets. For larger pallet options, there is a multi-level RPS which holds either 14 or 21 pallets based on customer selection. With the A- and C-axis configuration, the RPS is situated in front of the machine for maximum floor space savings. The operator has a full view of the work area and access to the CNC controller from the side of the machine, in addition to a load/unload station with cell controller. The RPS cell controller works at a higher level than the AWC controller and is adaptable to a higher range of functions, as well. The RPS is an ideal automation option when floor space is limited.
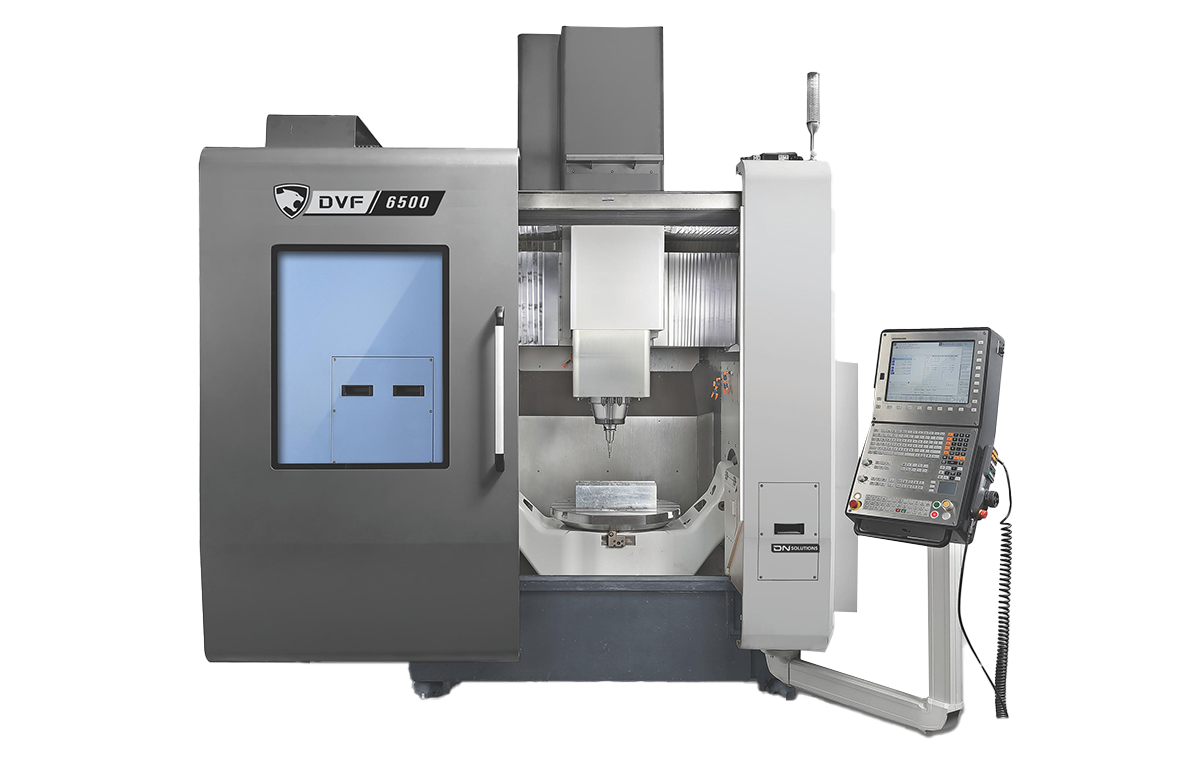
DVF 8000
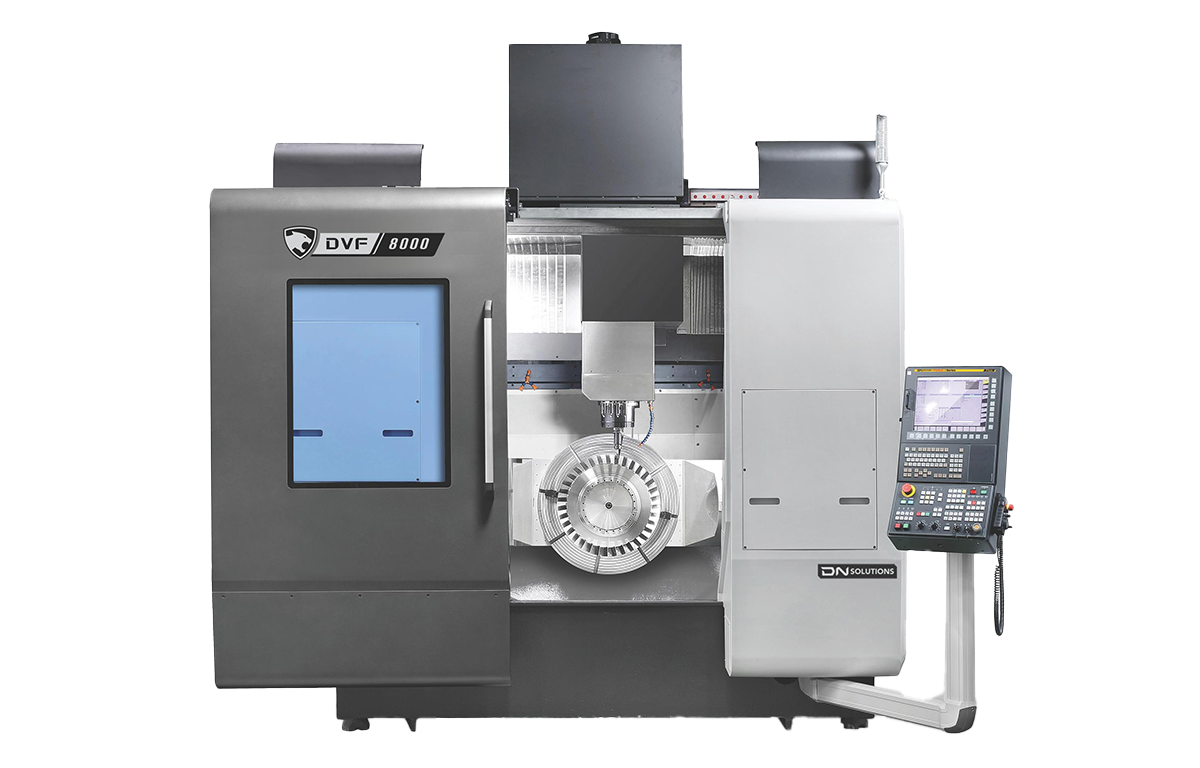
The DN Solutions (formerly Doosan Machine Tools) DVF 8000 shares many of the features of the DVF 5000, but is far bigger and has a much different structure. It incorporates dual ballscrews and motors on the Y-axis and dual motors driving the A-axis, along with a direct drive C-axis. It has a larger (800mm diameter) rotary table that supports a maximum weight of 3,086 lbs.
Automation Partner: You’ll frequently see a DVF 8000 in combination with the Linear Pallet System (LPS). It’s often preferred because it can be expanded all the way up to 80 pallets, based on your needs. The cell controller on the LPS is a PC-based open architecture that controls the entire system. You can load programs, work offsets and schedules. The controller will send everything to the machine. It will also integrate to an ERP system and generate utilization, efficiency and error reports. Human intervention is minimal.
The LPS is also capable of making smart decisions, especially regarding tool management of each machine in the line. If there isn’t enough life in the tool, it will flag the job, hold it in queue and move on to next job in the schedule. It can arrange jobs according to FIFO, JIT or earliest due date. If there’s a problem with any machine, LPS can go into a holding mode and then continue when the problem is resolved.
Another advantage of the LPS is that it can accommodate different types of machines. For example, you could have a DVF 8000 and NHM 6300 horizontal machining center in the same line with interchangeable pallets. This would potentially allow you to handle a roughing operation on the NHM 6300, and then have that part go into the DVF 8000 for a different operation.
Mix and Match
Of course, these are only a few examples of the combinations you can put together based on your needs and plant environment. The AWC is the choice for smaller shops just getting into automation, RPS for those that are limited with floor space and can’t accommodate an LPS, and the LPS is for anyone who needs all the bells and whistles with the option to expand in the future.
DN Solutions (formerly Doosan Machine Tools) stocks equipment with all three automation systems, so they are available for immediate delivery in many cases. These machines are equipped with 120-tool magazines to give you enough tools to efficiently process all your extra pallets with one setup.
Throughput. Labor Reduction. JIT.
Automation is all about maximizing spindle utilization. What if you could get close to a complete part family out a 5-axis pallet system by running multiple operations with one setup? If you factor in the workholding options available today, which allow you to make multiple parts per pallet, your output can double or triple.
Reducing human intervention also pays big productivity dividends. Any time a person is tending to a machine, you have non-productive time. Automation frees operators to manage multiple machines, perform other duties or maintain a better work/life balance.
Combining 5-axis with automation gives you the flexibility to react quickly and provide quick turnaround times. Don’t tie up capital by stockpiling parts “just-in-case.” Satisfy immediate customer needs without keeping a large inventory of part numbers that may not move for months.
If you have any questions on how 5-axis machining and automation can add value to your organization, please contact the Ellison Technologies team. We’d be glad to help.