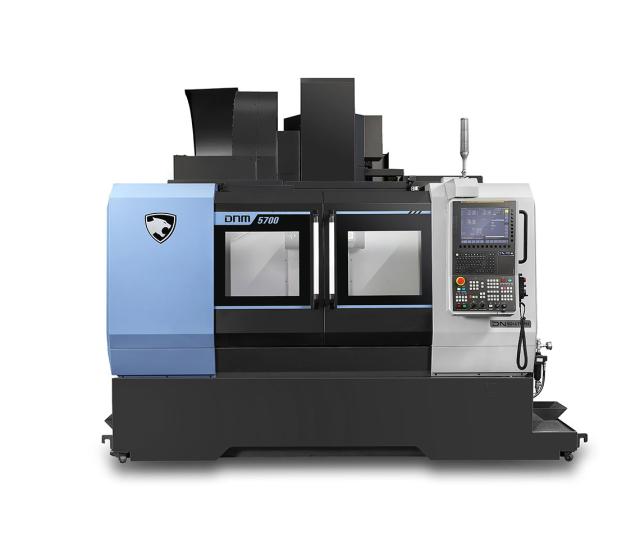
DNM Series
The DNM Series delivers the most value for your investment as the best-in-class vertical machining center fully equipped with the most standard features built-in. This powerfully productive machine features a BIGPLUS spindle, dual chip augers, FANUC 0i-M controls with DN Solutions (formerly Doosan Machine Tools) Easy Operation Package (EOP), through-spindle coolant, spindle chiller, and more. Get the machine that will give you the power to MAKE MORE.
-
Travel Distance X-axis1050 mm (41.3 in.)
-
Travel Distance Y-axis570 mm (22.4 in.)
-
Travel Distance Z-axis510 mm (20.1 in.)
-
Rapid Traverse X-axis36 m/min. (1417 in./min.)
-
Rapid Traverse Y-axis36 m/min. (1417 in./min.)
-
Rapid Traverse Z-axis30 m/min. (1181 in./min.)
-
Table Size1300 x 570 mm (51.2 x 22.4 in.)
-
Max Load1000 kg (2205 lbs.)
-
Spindle to Table Distance150 - 660 mm (5.9 - 26 in.)
-
Torque118/286 Nm (87/211 ft-lbs.)
-
Speed8000 rpm
-
Power15/18.5 kW (20/25 Hp)
-
ShankBIG PLUS CAT40
-
Changer Capacity30 (Opt. 40/60)
-
Max Diameter⌀80/125 mm (3.2/4.9 in.)
-
Max Length300 mm (11.8 in.)
-
Length3145 mm (123.8 in.)
-
Height2985 mm (117.5 in.)
-
Width2221 mm (87.4 in) + 1128 mm (44.4 in.)
-
Weight6500 kg (14330 lbs.)
Explore the DNM Series Lineup
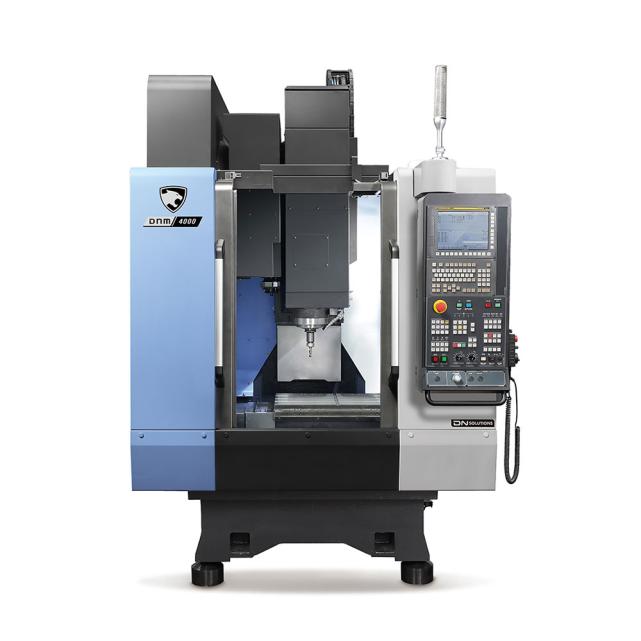
DNM 4000
Spindle Taper: CAT 40
Spindle RPM: 12,000 RPM
X Axis Travel: 20.5"
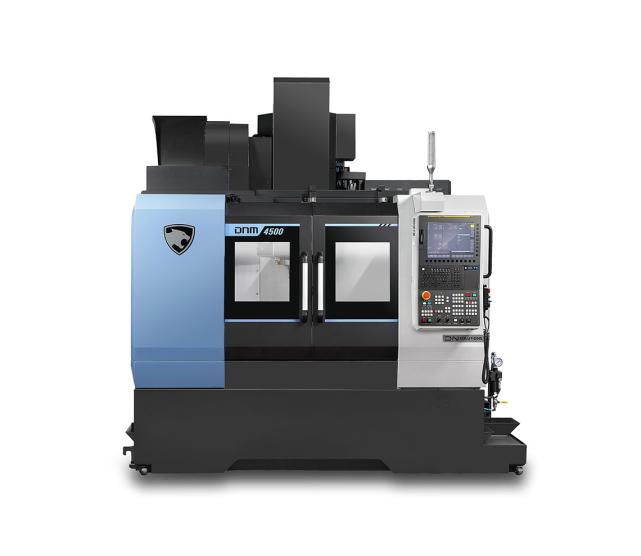
DNM 4500 4th GEN
Spindle Taper: CAT 40
Spindle RPM: 8,000 RPM
X Axis Travel: 31.5"
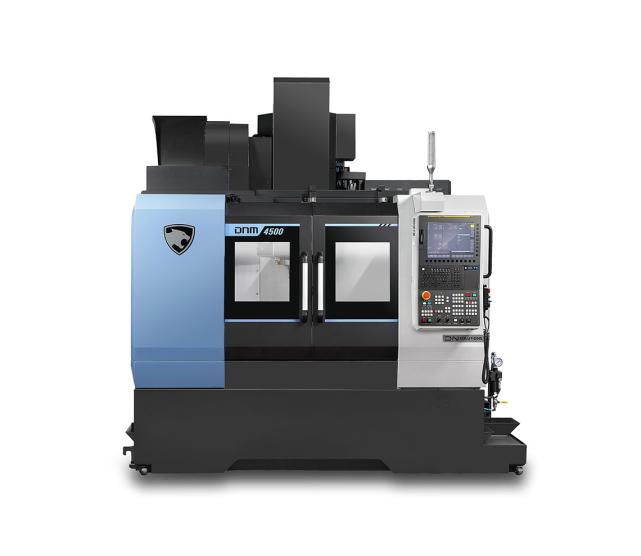
DNM 4500S 4th GEN
Spindle Taper: CAT 40
Spindle RPM: 15,000 RPM
X Axis Travel: 31.5"
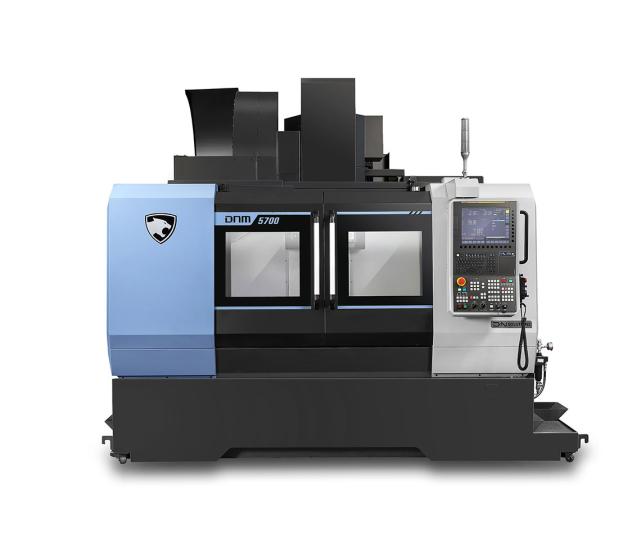
DNM 5700 4th GEN
Spindle Taper: CAT 40
Spindle RPM: 8,000 RPM
X Axis Travel: 41.3"
Build a Quote
1. SUBMIT FORM 2. CHECK YOUR EMAIL 3. CLICK EMAIL LINK TO BUILD YOUR PERSONALIZED QUOTE
Engineered for Rigidity, Power, and Volume Machining
The DNM 5700 4th Generation represents the latest evolution in DN Solutions' best-selling vertical machining center platform. Built for cutting large, heavy parts with repeatable precision, it delivers powerful spindle performance, large-axis travels, and industry-leading chip control. The 5700’s Meehanite cast-iron bed, oversized linear roller guides, and reinforced saddle design ensure exceptional stability—even under full-load, high-speed machining conditions. With X/Y/Z travels of 1,050 × 570 × 510 mm, and a 1,000 kg (2,205 lb) load capacity, it accommodates large part production without compromising surface finish or tool life.
DN SOLUTIONS (FORMERLY DOOSAN MACHINE TOOLS) DNM VERTICAL MACHINING CENTER ALL-PURPOSE PRODUCTION
Work smarter, not harder. The DN Solutions (formerly Doosan Machine Tools) DNM 5700 vertical machining center comes packed with the most production improving standard features to keep you one step ahead of the competition. Enhanced FANUC controls, pre-wired Renishaw probing, dual screw chip auger, through spindle coolant, spindle chiller, and Big Plus spindle to name a few.
Doosan DNM Series
Versatile Spindle Options: Torque or Speed
Choose between two powerful spindle configurations:
8,000 RPM high-torque spindle: 286 Nm (211 ft-lbs), 15/20 hp—ideal for hard metal removal
15,000 RPM high-speed spindle: 118 Nm (87 ft-lbs), 25 hp—perfect for precision contouring and mold work
Both spindles feature Big Plus CAT40 tooling and are oil-jacket cooled for thermal stability. Spindle acceleration and deceleration are tightly controlled, optimizing productivity while minimizing wear. Rigid tapping and through-spindle coolant come standard, ensuring better chip evacuation and part finish at higher feedrates.
Expandable Tooling and Intelligent Automation
The servo-driven double-arm ATC supports 30, 40, or 60 tools, each up to 300 mm long and 8 kg in weight. Chip-to-chip tool change time is just 4.1 seconds, improving cycle efficiency. Combined with Renishaw probe readiness, adaptive feedrate control, and tool load monitoring, the DNM 5700 is automation-ready—ideal for high-mix, low-touch environments. Smart features like manual pulse generator, full guarding, and large sliding doors simplify operator interaction and maintenance.
Smart Thermal and Load Control for Accuracy
Ellison’s DNM 5700 integrates Smart Thermal Monitoring, a sensorless algorithm that proactively compensates for spindle heat expansion. Combined with high-rigidity ball screws and roller guides, the system ensures micron-level repeatability during extended runs. Meanwhile, the Tool Load Monitoring System protects against tool breakage and wear, reducing unplanned downtime and improving tool utilization.
FAQ Section
What’s the difference between the 8K and 15K spindle options?
The 8,000 RPM high-torque spindle delivers up to 286 Nm of torque—ideal for heavy-duty cutting and harder metals like steel and cast iron. The 15,000 RPM spindle offers high-speed precision, better suited for aluminum, plastics, or complex 3D contouring in mold and die work. Your choice depends on part material, surface finish goals, and machining strategies.
How does the DNM 5700 improve thermal stability?
The machine uses a spindle oil chiller and software-based Smart Thermal Monitoring system to actively reduce thermal drift. Instead of relying on sensors, the algorithm compensates based on RPM and cycle duration—improving part accuracy during long or continuous jobs. This is especially valuable in aerospace and mold manufacturing, where tight tolerances are critical.
Is this machine automation-ready?
Yes. The DNM 5700 includes standard features that enable easy automation:
Probe-ready with Renishaw OMI-2T
Through-spindle coolant and air
Full enclosure with large access doors
Chip conveyors, tool load monitoring, and grease lubrication
These make it suitable for pallet systems, robotic loading, or lights-out manufacturing environments.
Can the ATC handle long or heavy tools?
Yes. The automatic tool changer supports tools up to 300 mm (11.8") long, 8 kg (17.6 lb) in weight, and up to 125 mm diameter (when adjacent pockets are empty). Options for 40- or 60-tool magazines allow greater flexibility in complex jobs or multi-material production lines.
What industries is the DNM 5700 built for?
This model is engineered for aerospace, die/mold, energy, medical, and general precision machining. Its rigidity, expanded travels, and thermal compensation features make it perfect for shops needing high mix, medium volume production with minimal setup time.
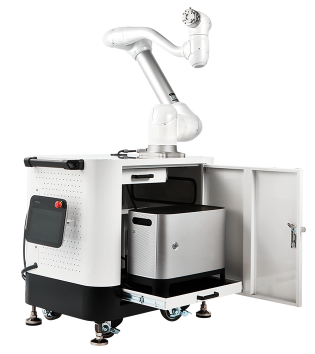
Collaborative Robots
Collaborative Robots
Doosan’s collaborative robots increase your machining productivity & make automation simple.
- Easy Set-up & Implementation
- Quick & Intuitive Programming
- Handle all types of Applications & Environment
- Works well with others; or great to fill a labor gap
Includes: Cobot, Mobile Base and Cockpit Control.
TURNKEY ENGINEERING SOLUTIONS
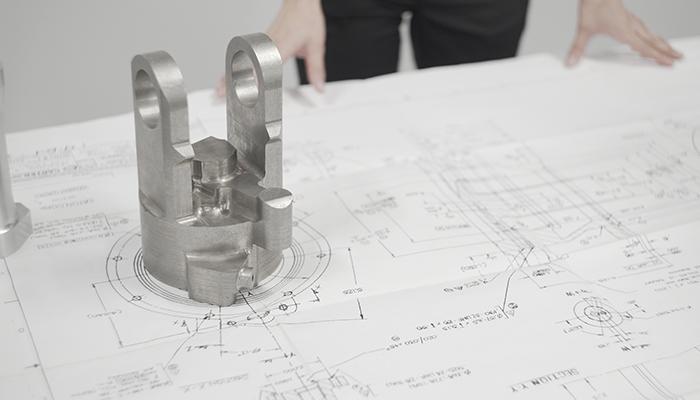
If you need to:
- Make a part faster
- Adapt your staff or parts to a new machine
- Program a new part
- Utilize the full potential of your machine
Our team of machining experts offer a wide range of Turnkey Solutions to help you make more out of your parts and your machine.