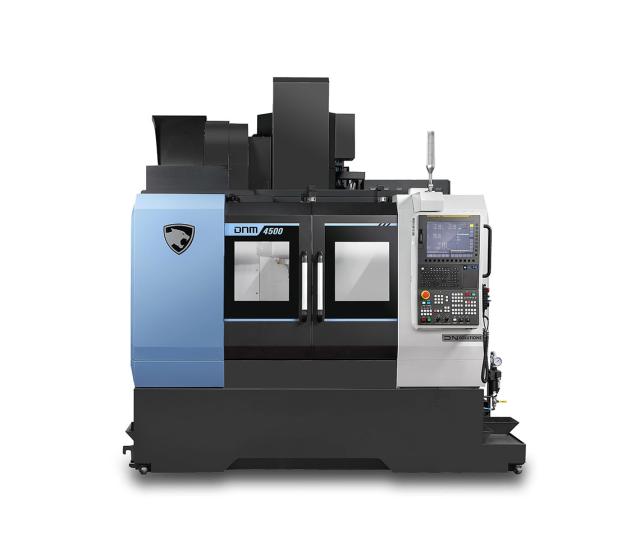
DNM Series
The DNM Series delivers the most value for your investment as the best-in-class vertical machining center fully equipped with the most standard features built-in. This powerfully productive machine features a BIGPLUS spindle, dual chip augers, FANUC 0i-M controls with DN Solutions (formerly Doosan Machine Tools) Easy Operation Package (EOP), through-spindle coolant, spindle chiller, and more. Get the machine that will give you the power to MAKE MORE.
-
Rapid Traverse X-axis36 m/min. (1417 in./min.)
-
Rapid Traverse Y-axis36 m/min. (1417 in./min.)
-
Rapid Traverse Z-axis30 m/min. (1181 in./min.)
-
Travel Distance X-axis800 mm (31.5 in.)
-
Travel Distance Y-axis450 mm (17.7 in.)
-
Travel Distance Z-axis510 mm (20.1 in.)
-
Table Size1000 x 450 mm (39.4 x 17.7 in.)
-
Max Load600 kg (1320 lbs.)
-
Spindle to Table Distance150 - 660 mm (5.9 - 26 in.)
-
Speed8000 rpm
-
Power18.5 kW (25 Hp)
-
Torque118/286 Nm (87/211 ft-lbs.)
-
Changer Capacity30 (Opt. 40/60)
-
Max Diameter⌀80/125 mm (3.2/4.9 in.)
-
Max Length300 mm (11.8 in.)
-
ShankBIG PLUS CAT40
-
Weight5000 kg (11023 lbs.)
-
Length2835 mm (111.6 in.)
-
Height2980 mm (117.3 in.)
-
Width2220 mm (87.4 in.)
Explore the DNM Series Lineup
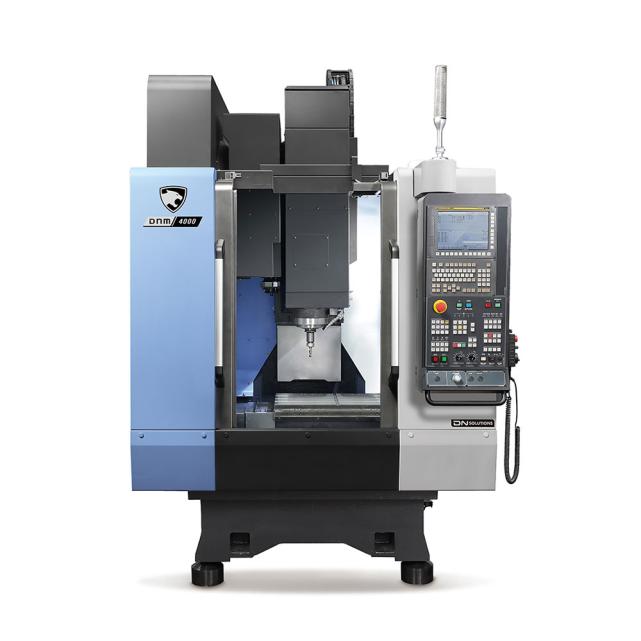
DNM 4000
Spindle Taper: CAT 40
Spindle RPM: 12,000 RPM
X Axis Travel: 20.5"
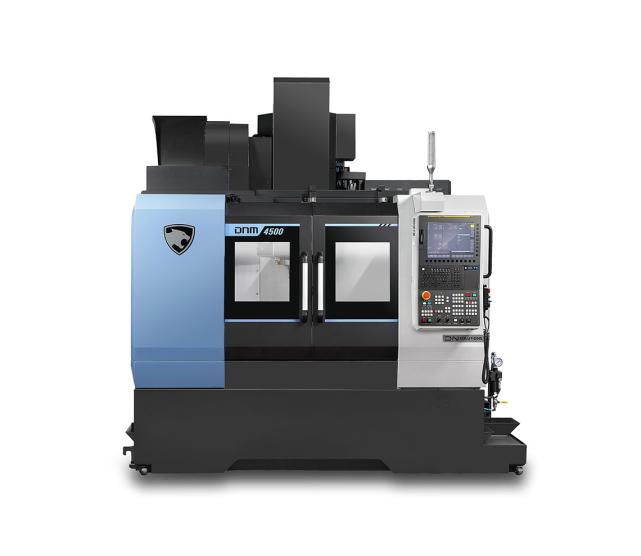
DNM 4500 4th GEN
Spindle Taper: CAT 40
Spindle RPM: 8,000 RPM
X Axis Travel: 31.5"
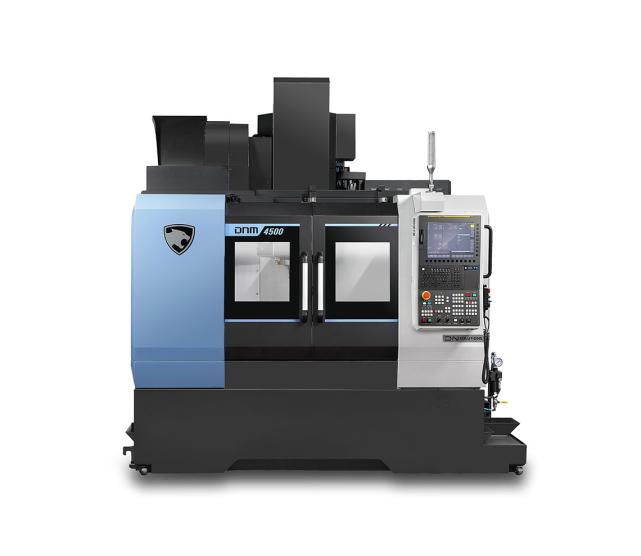
DNM 4500S 4th GEN
Spindle Taper: CAT 40
Spindle RPM: 15,000 RPM
X Axis Travel: 31.5"
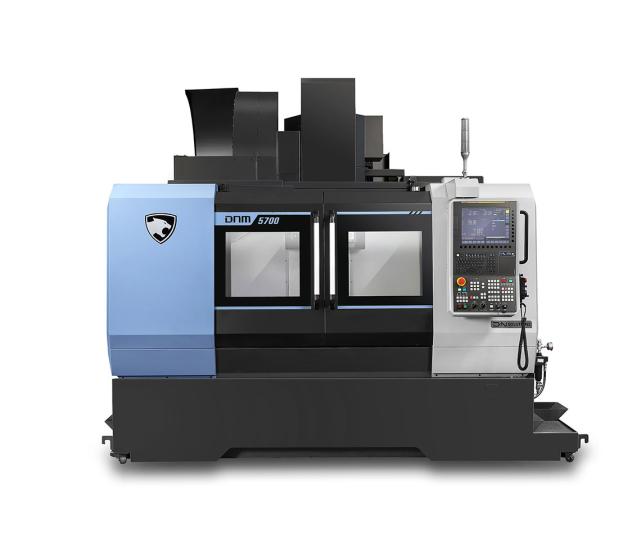
DNM 5700 4th GEN
Spindle Taper: CAT 40
Spindle RPM: 8,000 RPM
X Axis Travel: 41.3"
Build a Quote
1. SUBMIT FORM 2. CHECK YOUR EMAIL 3. CLICK EMAIL LINK TO BUILD YOUR PERSONALIZED QUOTE
Built for Precision, Designed for Productivity
The DNM 4500 4th Generation vertical machining center from DN Solutions elevates the proven DNM platform with enhanced rigidity, thermal control, and productivity features tailored for modern manufacturers. Equipped with a powerful direct-coupled spindle, upgraded roller linear guideways, and a compact yet robust frame, the DNM 4500 4th Gen is purpose-built for high-volume precision work in aerospace, medical, toolmaking, and general part production. Its improved thermal stability, rapid traverse speeds, and advanced monitoring systems ensure consistent accuracy, even under continuous load.
Flexible Spindle Options for Varying Application Demands
The machine comes with a choice of high-torque or high-speed spindles:
8,000 RPM Spindle: 11/15 kW (15/20 hp), 286 Nm torque – ideal for heavy-duty machining
15,000 RPM Spindle: 11/18.5 kW (15/25 hp), 118 Nm torque – ideal for high-speed finishing
Both spindle systems use a Big Plus CAT 40 taper with a direct-coupled design and oil-jacket chiller for excellent thermal control. Acceleration and deceleration times are fast (under 3.5 seconds), improving throughput while maintaining surface integrity.
Expanded Tool Capacity and Intelligent Automation
The DNM 4500 4th Gen supports:
30, 40, or 60-tool servo-type, double-arm ATCs
Tool-to-tool change time: 1.2 seconds
Chip-to-chip change time: 4.1 seconds
Max tool size: 125 mm dia. (with adjacent pots empty), 300 mm length, 8 kg weight
Tool life is extended with adaptive feedrate control and tool load monitoring, which dynamically adjust feedrates and trigger alarms in case of tool wear or breakage. The machine is also Renishaw probe-ready, supporting in-process part and tool measurement for automated cells.
Structure and Motion for Consistent Cutting Performance
The rigid Meehanite cast iron bed, wide roller linear guideways (X: 34 mm, Y/Z: 45 mm), and oversized 40 mm ball screws ensure excellent vibration dampening and cutting stability. Preloaded, pre-tensioned drive systems and directly coupled servo motors eliminate backlash.
Key motion specs:
Travels (X/Y/Z): 800 / 450 / 510 mm
Rapid traverse: 42 m/min (X/Y), 36 m/min (Z)
Positioning accuracy: ±0.008 mm (X/Z), ±0.007 mm (Y)
Repeatability: ±0.005 mm (X/Z), ±0.004 mm (Y)
Thermal Compensation and Chip Management
To ensure stability in long cycle times, the DNM 4500 includes:
Smart Thermal Monitoring: Predicts spindle expansion using speed-based algorithms
Oil-Jacketed Spindle Chiller: Reduces thermal drift
Tool Load Monitoring System: Detects overloads and breakage
Flood coolant with through-spindle cooling (215–225 psi)
Screw-type chip conveyors and 100-gallon coolant tank
These features contribute to repeatable accuracy and lights-out compatibility, even under varying shop conditions.
Compact, Operator-Friendly Machine Design
Despite its rigidity and power, the DNM 4500 4th Gen remains operator-focused:
Machine footprint: 2,220 x 2,835 mm (87 x 112 in)
Machine height: 2,980 mm (117 in)
Large sliding doors (980 mm opening) for overhead crane access
MPG pendant with 10-foot cord and magnetic mount
Portable spindle chiller, telescoping covers, eco grease lube system
The standard FANUC 0i-Plus with iHMi touchscreen simplifies operation, and built-in protections like chip shields and splash guards ensure safe use in high-duty-cycle environments.
FAQ Section
What are the main differences between the 8K and 15K spindle options?
The 8,000 RPM spindle delivers higher torque (286 Nm), ideal for heavy-duty roughing and tougher materials. The 15,000 RPM option is better for high-speed finishing and aluminum work, offering smoother surface finishes and tighter tolerances. Both include direct-coupled drives, rigid tapping, and oil-cooled jackets for thermal control.
How does Smart Thermal Monitoring improve machining accuracy?
Smart Thermal Monitoring uses algorithmic models based on spindle speed to estimate and compensate for thermal drift. It adjusts axis positions to counteract spindle elongation from heat, helping maintain precise tolerances across long machining cycles—especially beneficial for aerospace and medical parts where microns matter.
Can the DNM 4500 4th Gen be automated for lights-out production?
Yes. The machine includes probe-ready Renishaw optics, automatic tool monitoring, and adaptive feedrate control—all essential for unattended machining. Its chip evacuation system, coolant management, and durable enclosure further support lights-out workflows in high-mix environments.
What kind of tool changers are available, and how do they impact productivity?
You can choose from 30, 40, or 60-tool ATCs. The 60-tool setup is recommended for high-mix or multi-operation work. With a 1.2-second tool-to-tool change and 4.1-second chip-to-chip cycle, the machine minimizes downtime and increases spindle utilization—key for shops looking to improve throughput.
Is the DNM 4500 a good fit for tight shop floors?
Yes. Despite its rugged construction, the machine has a compact footprint of 87" x 112", making it an excellent fit for cellular manufacturing or tight production floors. Its overhead access, front chip disposal, and compact coolant system reduce operator strain and allow flexible layout design.
Want to Learn More?
Fill out the form to connect with a machining expert and get detailed information on the DNM 4500 4th Gen. Whether you need specs, pricing, or application guidance, we’re here to help you find the right solution for your shop.
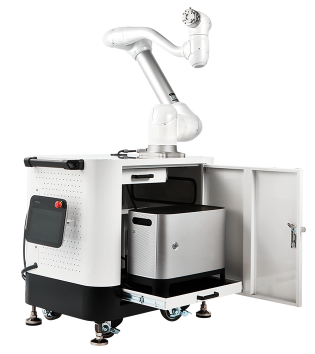
Collaborative Robots
Collaborative Robots
Doosan’s collaborative robots increase your machining productivity & make automation simple.
- Easy Set-up & Implementation
- Quick & Intuitive Programming
- Handle all types of Applications & Environment
- Works well with others; or great to fill a labor gap
Includes: Cobot, Mobile Base and Cockpit Control.
TURNKEY ENGINEERING SOLUTIONS
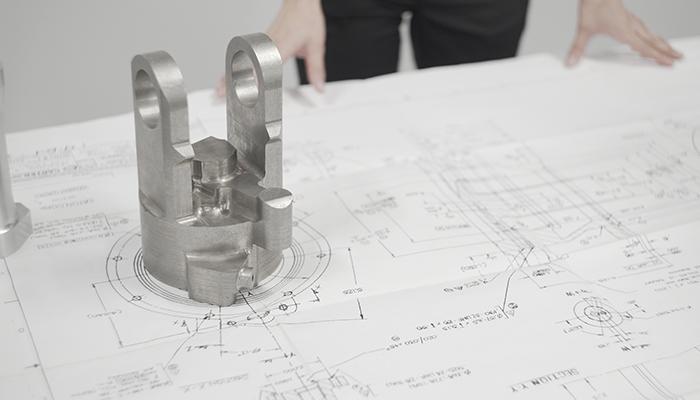
If you need to:
- Make a part faster
- Adapt your staff or parts to a new machine
- Program a new part
- Utilize the full potential of your machine
Our team of machining experts offer a wide range of Turnkey Solutions to help you make more out of your parts and your machine.