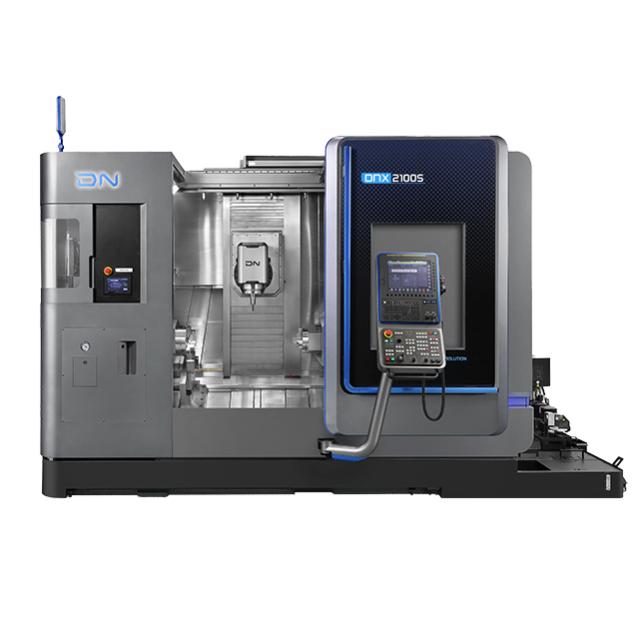
DNX Series
The DNX Series is a compact multitasking solution that integrates dual spindles and a B-axis with a powerful milling spindle, allowing for high-precision machining in a small footprint. It’s ideal for shops needing to maximize productivity and part complexity without sacrificing space or accuracy.
-
Spindle Speed5,000 rpm
-
Spindle Power18.5 kW (25 hp)
-
Spindle Torque326 Nm (240 ft-lb)
-
Chuck size210 mm (8 in.)
-
Max. Turning Diameter520 mm (21 in.)
-
Max. Turning Length1100 mm (43 in.)
-
Width2285 mm (90 in.)
-
Weight10500 kg (23149 lb.)
-
Length4615 mm (182 in.)
-
Height2630 mm (104 in.)
-
Max. Spindle Speed12,000 r/min (12,000 RPM)
-
Max. Spindle Power18.5/15 kw (25/20 hp.)
-
Max. Spindle Torque58 Nm (42 ft-lb)
High-Performance Multi-Tasking in One Setup
The DNX 2100 is a high-precision, multi-axis mill-turn machining center engineered for complex part production in a single setup. With full contouring on the C-axis, a 240° tilting B-axis, and Y-axis travel of ±4.525 inches, it enables complete 5-axis milling and turning capabilities on one platform. Whether you're machining cross-holes, off-center features, or intricate geometries, the DNX 2100 delivers the accuracy, repeatability, and cycle time reduction required for today’s demanding production environments. It is ideal for aerospace, medical, energy, and contract manufacturing.
DNX 2100S High-performance turn-mill Multi-taking machine
DNX 2100S Barrel Machining - DN Solutions
Rigid Structure with Advanced Thermal Stability
Built on a heavily ribbed, one-piece cast iron bed, the DNX 2100 resists vibration and deformation even during aggressive cutting. Heavy-duty linear roller guideways provide smooth, fast movement and tight positional tolerances. Multiple thermal compensation sensors are strategically placed throughout the structure and spindle for real-time thermal drift control. The spindle chiller system ensures consistent performance during extended machining cycles, while the servo-driven tailstock maintains centerline alignment under variable load conditions.
Milling and Turning Spindles Engineered for Power
The DNX 2100 features two powerful spindles:
Main turning spindle: 5,000 RPM, 22 kW (30 hp), 326 Nm torque
Milling spindle: 12,000 RPM, 18.5 kW (25 hp), 58 Nm torque
The spindles are integral motor designs with beltless drive for maximum torque transmission, rapid acceleration, and zero backlash. The C-axis enables 360° contouring and turning, while the B-axis offers 240° of tilt for angled milling or compound hole drilling. These capabilities allow the DNX 2100 to handle multi-process parts without repositioning.
Intelligent Tooling and Y-Axis Flexibility
Equipped with a 30-tool automatic tool changer (ATC)—expandable to 60 tools—the DNX 2100 uses a CAPTO C6 interface, allowing quick tool changes with high rigidity. The ATC features random tool selection and a 1.7-second tool-to-tool time for fast cycle transitions. The orthogonal Y-axis enables true off-center machining, with the ability to mill flats, drill off-axis holes, and finish keyways without custom rotary tools. This greatly reduces setup times and fixture complexity.
Integrated Coolant, Probing, and Automation Features
To support unattended operation and increase tool life, the DNX 2100 comes with:
20 bar (290 psi) high-pressure coolant system
Air blast for chuck cleaning
Automatic tool setter with 4-direction touch sensors
Chip conveyor and 105-gallon coolant tank
Grease lubrication system with cartridge-based refills
Safety enclosure with interlocks and signal tower
Its FANUC 0i-TF Plus control includes a 15” touch panel, 2 MB part storage, USB/Ethernet connectivity, and EZ Guide i conversational programming.
FAQ Section
What are the key benefits of the DNX 2100’s multi-axis configuration?
The DNX 2100 combines turning, milling, Y-axis, B-axis, and full contouring C-axis control in a single platform. This configuration allows for full part completion—including angled features and off-center milling—in one setup, drastically reducing changeovers, fixture complexity, and tolerance stack-up. It’s ideal for shops aiming to improve throughput on complex parts without compromising on precision.
How does the thermal compensation system improve machining accuracy?
Thermal growth can significantly affect machining accuracy during long or high-speed cycles. The DNX 2100 uses a multi-point thermal compensation system with sensors placed on the structure and milling spindle. This allows real-time adjustments that reduce dimensional drift, ensuring stable machining conditions for tight-tolerance work. Paired with oil chillers and integral spindle design, the machine maintains accuracy even under demanding conditions.
What kind of workpieces is the DNX 2100 best suited for?
The DNX 2100 is built for parts requiring multiple machining operations—turning, milling, cross-hole drilling, or angled features. Typical applications include medical implants, aerospace bushings, powertrain components, and hydraulic fittings. Its B-axis tilt and Y-axis travel make it well-suited for complex geometries and features that would otherwise require multiple setups or specialty tooling.
Is the DNX 2100 suitable for lights-out manufacturing?
Yes. With features like automatic tool setting, chip evacuation system, high-pressure coolant, and a fully enclosed work area, the DNX 2100 supports unattended machining. The machine’s robust control software includes tool monitoring, alarms, and safety interlocks that help protect the spindle, tooling, and part during automated cycles. An optional parts catcher is also available for finished part removal without operator intervention.
What is the control interface like for operators?
The DNX 2100 uses a FANUC 0i-TF Plus control with a 15” touchscreen interface, intuitive layout, and EZ Guide i conversational programming. It includes support for custom macros, multiple canned cycles, tool monitoring, program protection, and USB/Ethernet transfer. It’s engineered for both experienced G-code programmers and operators familiar with conversational control environments
DNX Series:
Vertical Machining Centers for High Precision and Productivity
The DNX Series from Doosan brings cutting-edge technology to the realm of vertical machining, offering impressive performance and precision for a wide range of applications.
- DNX 2100: Compact, high-performance vertical machining center designed to handle both precision and speed. With an optimal spindle speed and rapid traverse rates, the DNX 2100 is ideal for manufacturers seeking efficient production with tight tolerances.
Key Benefits
- Increased Productivity: Designed for both high-speed and high-precision applications, allowing for faster cycle times.
- Enhanced Precision: Ideal for industries demanding tight tolerances and superior finishes.
- User-Friendly Control: The advanced CNC control system simplifies operation, improving setup times and overall workflow efficiency.
- Optimized for a Variety of Industries: Perfect for automotive, aerospace, and precision engineering applications.