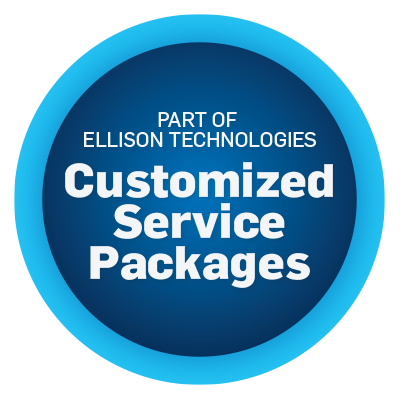
Do you know how much unexpected downtime is costing you?
Your business depends on your machines for quality parts and manufacturing success: Ensure Their Strength.
Unplanned maintenance downtime costs your business THOUSANDS OF DOLLARS. You can avoid potential risks with a Preventive Maintenance (PM) Program. PM programs are designed to maximize the overall amount of cutting time and to ensure that machines continuously operate at quoted specifications for accuracy and repeatability.
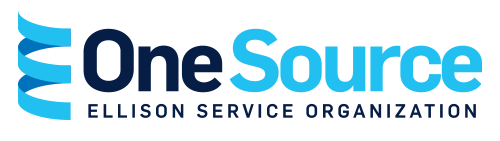
Contact Us Today To Get Started
Reach out to one of Ellison's OneSource service account experts to get more details.